What is Root Cause Analysis (RCA) in Maintenance and Why It’s Important
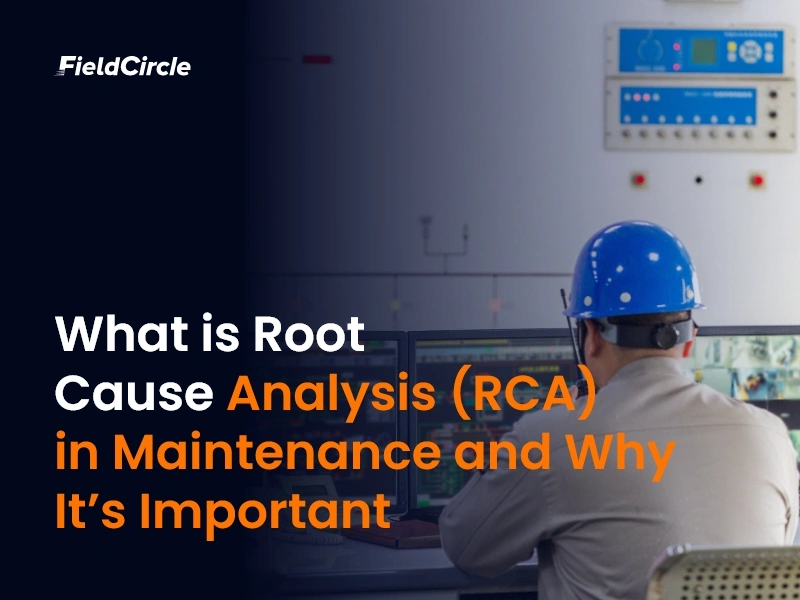
Recurring problems lead to unplanned downtime, higher maintenance costs, safety risks, and stress on the maintenance crew.
When underlying issues go unresolved, they come back to bite when you least expect it – maybe in the middle of a critical production run or when you’re short-staffed. It can feel like you’re spinning your wheels, treating symptoms but never curing the disease.
Root cause analysis (RCA) is a methodical process to dig deep and uncover the true cause of a problem, so you can fix it once and for all. In maintenance, performing RCA means the difference between temporary fixes and lasting solutions. This article will explain what RCA is in the context of maintenance, and why investing time in RCA pays off immensely through improved reliability, reduced downtime, and a more efficient operation.
What is Root Cause Analysis (RCA) in Maintenance?
Root cause analysis is exactly what it sounds like: analyzing a problem to find its root cause. In maintenance, it’s an approach to identify why a failure or issue occurred, not just what failed. Instead of just swapping out a broken part and moving on, RCA urges you to ask, “Why did this part break? What set of circumstances caused this failure?”
Key aspects of RCA:
- It’s a systematic process that follows a structured, step-by-step approach. There are various techniques (like the 5 Whys, fishbone diagrams (Ishikawa diagrams), Pareto analysis, fault tree analysis, etc.) that are used in RCA. All they aim to drill down from the problem to underlying causes.
- It often involves collecting maintenance data (failure history, maintenance records, operating conditions at time of failure) and possibly examining failed components in detail.
- It usually requires some cross-functional input. For example, you might involve operations (to understand how the machine was being used), engineering (to consider design issues), and maintenance (to review past fixes).
-
The goal is to find one or more root causes – there can be multiple – which, if addressed, will prevent the issue from recurring. This is often summarized as finding the point in the cause-and-effect chain where you can intervene to prevent the failure.
Why is Root Cause Analysis Important?
Performing RCA requires effort and time – so why is it worth it? Discussed are the key reasons that explain why RCA is critically important in maintenance:
1. Prevent Recurring Failures and Reduce Downtime
This is the most obvious benefit. If you identify the root cause of a problem and eliminate it, the problem should not recur. This can drastically reduce unplanned downtime. Recurring failures are a huge hit to reliability metrics like Mean Time Between Failures (MTBF). By tackling root causes, you increase MTBF, meaning equipment stays up longer between incidents.
Root cause analysis (RCA) not only addresses the immediate issue but also helps to uncover systemic problems that may be affecting the long-term stability of systems or processes. In many cases, recurring failures stem from overlooked or misdiagnosed underlying issues, which, when left unresolved, can lead to costly disruptions. Organizations can make use of maintenance software to perform RCA and successfully pinpoint the exact cause of failures and implement permanent corrective actions instead of relying on temporary fixes.
2. Cost Savings on Maintenance and Parts
Recurring problems are expensive:
-
Spare parts consumption: Consumption of spare parts goes up if you’re repeatedly replacing components. RCA might reveal you’re replacing the wrong part or not addressing why it fails. Fixing the potential cause could mean you don’t have to buy that part repeatedly.
-
Labor costs: The maintenance team’s time is spent better on preventive work or new projects rather than fixing the same issue again and again. By solving the root issue, you free up labor for more value-added activities.
-
Collateral damage: Sometimes, a small recurring issue can lead to bigger failures. For example, if a bearing keeps failing and you just replace it each time without RCA, one day that could escalate to a seized shaft or damaged motor – a much costlier fix. Solving it early prevents expensive secondary failures.
3. Improved Safety
Recurring equipment failures aren’t just an operational nuisance – they can be a safety hazard. Performing RCA to eliminate chronic failures also eliminates repeated exposure of workers to that hazard or repair task.
Moreover, RCA is a cornerstone of a safety incident investigation. If an equipment failure caused or nearly caused an accident, you must do RCA to prevent it from causing harm next time. Many organizations blend their safety investigations and maintenance RCA processes for this reason.
4. Better Product Quality
Maintenance directly affects the quality of output. Suppose a temperature control problem in a reactor causes occasional off-spec products. An RCA might find the root cause (perhaps a sensor drift or a control algorithm issue). Fixing that ensures the process conditions remain in the sweet spot, leading to more consistent product quality.
Also, unstable equipment tends to produce more defects. Think of a packaging line that frequently misfeeds – those episodes might create a bunch of incorrectly sealed packages (waste). Solve the cause of misfeeds and you not only stop the downtime, but also reduce the waste and quality rejects.
Thus, RCA contributes to quality improvement efforts. In fact, many quality management approaches (like Six Sigma or ISO 9001 corrective action processes) demand root cause analysis of defects.
5. Informed Decision-Making (Repair vs Replace, Design Changes)
In essence, RCA provides knowledge. It turns “unknown unknowns” into “known issues we can manage.” Maintenance managers are thus in a position to justify improvements or investments with evidence. Ultimately, when they understand root causes, they’re better equipped to brainstorm and make smarter long-term decisions:
-
Replace or Redesign: If RCA reveals that a machine has a fundamental design flaw or is undersized for the workload, you might decide to replace it with a better one. Without RCA, you might keep pouring money into patching it.
-
Maintenance Strategy Adjustments: RCA might tell you that your preventive maintenance isn’t effective. For instance, if the root cause was lack of lubrication in a bearing, maybe you need to increase lubrication frequency or improve the method. It could drive changes in PM schedules or tasks to address what you learned.
-
Training Needs: Sometimes the root cause is human error or lack of skill (e.g., improper installation technique leading to misalignment). This highlights a need for training or procedural changes.
- Spare Parts Inventory: If a root cause is identified and fixed, you might reduce or eliminate the need to stock certain spare parts. Or vice versa, if RCA indicates a particular part will always be failure-prone during certain conditions, you might stock more or upgrade it.
6. Fostering a Proactive, Problem-Solving Culture
Emphasizing root cause analysis in your maintenance team fosters a mindset of continuous improvement. Technicians start thinking beyond the immediate fix; they become more curious about why something failed. Over time, this elevates the whole team’s problem-solving skills.
Instead of celebrating that “we got the line back up in 30 minutes,” the culture shifts to “we fixed it and here’s what we’re doing to make sure that doesn’t happen again.” This can be very motivating – solving the puzzle of a chronic issue is satisfying, and seeing it not come back is even more rewarding.
When maintenance folks see management taking their RCA recommendations seriously and investing in fixes, it creates a positive feedback loop.
7. Alignment with Reliability Initiatives
If your organization is pursuing reliability-centered maintenance (RCM) or Total Productive Maintenance (TPM) or ISO 55000 asset management, RCA is a foundational element of those methodologies. RCM, for instance, requires understanding failure modes and effects analysis (FMEA) to determine the right maintenance strategy. TPM has a pillar for focused improvement which uses RCA to eliminate chronic losses.
By mastering RCA, maintenance teams contribute strongly to these higher-level programs. It moves maintenance from being seen as “fixers” to “improvers” of the process. For management, an RCA program can be tracked via metrics like reduction in repeat failures, which is a direct measure of improved reliability.
Conclusion
In maintenance, root cause analysis (RCA) is the key to breaking out of the reactive cycle. It shifts the approach from “fix and forget (until next time)” to “fix and learn (so there’s no next time)” and brings significant improvements to the maintenance management practice.
As a maintenance leader, encouraging and investing in RCA will pay dividends. Yes, it requires discipline to not just move on to the next task, and it may require training the team in analysis techniques. But the payoff is evidenced by countless success stories in industry where RCA has eliminated chronic downtime and chronic headaches. So, make it a norm to perform root cause analysis to remain at the forefront of maintenance excellence.