Boosting Efficiency in Manufacturing Industry Through CMMS
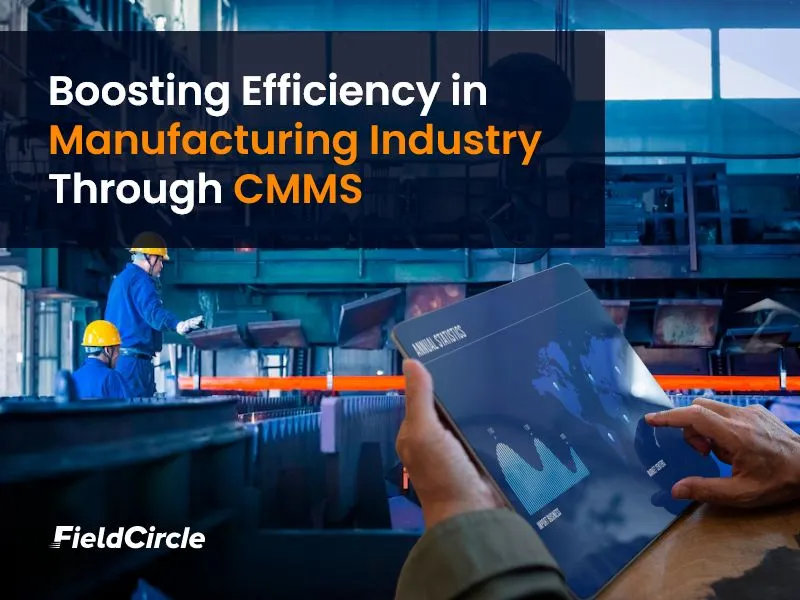
The sheer scope of maintenance activities in manufacturing facilities is vast and varied, as it encompasses everything, right from routine inspections to complex equipment overhauls. Manifold challenges grapple manufacturers who are always looking for ways to keep maintenance costs in control and sustain efficiency levels. So, manufacturing maintenance is an uphill task and creates a need for a dedicated maintenance software for manufacturing.
The significance of CMMS lies in its ability to centralize and automate maintenance tasks, ranging from scheduling preventive maintenance to tracking inventory and managing work orders. With the intricate machinery and equipment in manufacturing facilities, any downtime due to maintenance issues can result in significant financial losses and operational setbacks. For instance, unplanned downtime due to poorly maintained equipment costs industrial manufacturers an estimated $50 billion annually. But as said, CMMS is a one-stop solution for all these woes.
Going ahead, we shed light on CMMS, its functionalities, benefits, and elements. It will serve as a comprehensive guide for manufacturers looking to harness the power of CMMS. Read on.
How is CMMS Used in Manufacturing?
As a centralized platform, manufacturing CMMS (computerized maintenance management system) integrates into the manufacturing workflow by bringing in its scope every single process. They can set maintenance schedules based on equipment usage, runtime, or predefined intervals, so that inspections, lubrication, calibrations, and other preventive measures are performed at the right time.
When breakdowns occur, maintenance technicians can create work orders directly within the system, detailing the issue, required repairs, and any parts or resources needed. CMMS prioritizes these work orders based on urgency and assigns them to appropriate personnel for prompt resolution of equipment failures.
CMMS also serves as a repository for maintenance documentation and historical data. Maintenance logs, inspection reports, repair records, and equipment histories and all other documentation is stored in the system. Maintenance staff can tap these valuable insights and analyze maintenance trends and use them to build maintenance strategies.
Benefits of CMMS for Manufacturing Efficiency
Amongst the myriad benefits that manufacturing CMMS comes with, discussed below are benefits that you are going to definitely experience after its implementation:
Improved Equipment Uptime
In manufacturing, every minute of downtime equates to lost production and revenue. A CMMS in the manufacturing industry ensures that production equipment, such as assembly lines, CNC machines, and robotic arms, remain operational at peak efficiency.
By scheduling regular maintenance tasks, conducting predictive maintenance based on real-time equipment data, and swiftly addressing any issues, CMMS minimizes unplanned downtime. This allows manufacturing plants to meet production targets consistently, fulfill orders on time, and maintain a competitive edge in the market.
Efficient Maintenance Management
Manufacturing facilities encompass a vast array of machinery and equipment, each requiring precise and timely maintenance. CMMS streamlines maintenance management by automating workflows, optimizing scheduling, and centralizing maintenance-related data.
Maintenance teams can easily access work orders, equipment histories, and maintenance manuals, streamlining the execution of tasks. The idle time is minimized and maintenance resources are utilized effectively, which ultimately leads to smoother production processes and improvement in plant efficiency.
Inventory Control
Manufacturing operations rely on a diverse range of spare parts, consumables, and supplies to maintain equipment and support production activities. A CMMS helps manufacturing plants maintain optimal inventory levels by tracking usage, monitoring stock levels, and automating replenishment processes.
By accurately forecasting inventory needs based on maintenance schedules and historical usage data, CMMS prevents stockouts and overstocking situations. This ensures that critical spare parts are always available when needed, minimizing production disruptions and optimizing inventory costs.
Data-Driven Decisions
Data is the lifeblood of modern manufacturing, driving insights and informing strategic decisions. CMMS collects and analyzes vast amounts of data related to equipment performance, maintenance activities, and production downtime. Manufacturing managers can leverage this data to identify trends, pinpoint areas for improvement, and optimize maintenance strategies.
For example, analyzing equipment failure patterns can help identify recurring issues and prioritize preventive maintenance tasks, reducing downtime and increasing equipment reliability. By making data-driven decisions, manufacturing plants can enhance operational productivity, improve product quality, and stay ahead of the competition.
Regulatory Compliance
The manufacturing industry is subject to stringent regulatory requirements aimed at ensuring product quality, worker safety, and environmental protection. CMMS plays a crucial role in maintaining regulatory compliance by documenting all maintenance activities, inspections, and certifications.
Detailed maintenance records provide a comprehensive audit trail, demonstrating compliance with regulatory standards during inspections and audits. By ensuring compliance with regulations such as ISO standards or OSHA requirements, CMMS helps manufacturing plants avoid fines, penalties, and reputational damage, while safeguarding the well-being of employees and the environment.
Cost Reduction
Cost management is a top priority for manufacturing plants seeking to maintain profitability in a competitive market. CMMS contributes to cost reduction by optimizing maintenance processes, minimizing downtime, and controlling inventory costs. Preventive maintenance helps prevent costly breakdowns and extends the lifespan of equipment, reducing repair and replacement expenses.
Efficient maintenance management streamlines labor utilization and reduces overtime costs. Inventory control features prevent excess inventory and minimize carrying costs. By optimizing maintenance operations and controlling costs, CMMS helps manufacturing plants improve their bottom line and remain financially sustainable in the long term.
Key Features of CMMS for Manufacturers
Listed below are critical features that an all-inclusive manufacturing CMMS (computerized maintenance management system) offers:
Feature |
Role |
Equipment Hierarchies |
Organizes equipment in hierarchical structures to reflect the manufacturing process flow, enabling easier navigation and management of complex production systems. |
Predictive Maintenance |
Applies advanced analytics and sensor data to predict equipment failures before they occur, minimizing unplanned downtime and optimizing maintenance schedules. |
Production Scheduling |
Integrates with production planning systems to schedule maintenance activities during periods of low production demand, minimizing disruption to manufacturing operations. |
Spare Parts Optimization |
Analyzes historical usage data and equipment reliability to optimize spare parts inventory levels, ensuring critical components are available when needed without excess stock. |
Downtime Tracking |
Captures and analyzes downtime events to identify root causes and implement corrective actions to reduce downtime and improve overall equipment effectiveness (OEE). |
Quality Management |
Integrates with quality management systems to track maintenance activities related to quality issues, ensuring compliance with quality standards and regulations. |
Asset Performance Metrics |
Monitors key performance indicators (KPIs) such as mean time between failures (MTBF) and mean time to repair (MTTR) to assess equipment reliability and performance over time. |
Energy Management |
Monitors energy usage of manufacturing equipment and identifies opportunities for energy efficiency improvements through proactive maintenance and equipment optimization. |
Regulatory Compliance |
Ensures compliance with industry regulations such as ISO 9001 or FDA requirements by documenting maintenance activities, inspections, and certifications related to manufacturing processes. |
Work Instructions |
Provides digital work instructions and documentation to guide technicians through maintenance procedures, ensuring consistency and adherence to best practices in equipment servicing. |
Production Integration |
Integrates with production systems to capture real-time production data and correlate it with equipment maintenance activities, enabling better coordination between maintenance and production schedules. |
Failure Mode Analysis |
Conducts failure mode and effects analysis (FMEA) to identify potential failure modes of equipment components, prioritize maintenance tasks, and mitigate risks to production processes. |
Calibration Management |
Manages equipment calibration schedules and records to ensure accuracy and reliability of measurement and control instruments used in manufacturing processes. |
Root Cause Analysis |
Performs root cause analysis (RCA) on equipment failures to identify underlying causes and implement corrective actions to prevent recurrence, improving equipment reliability and reducing downtime. |
Safety Compliance |
Tracks maintenance activities related to safety-critical equipment and ensures compliance with safety regulations and standards such as OSHA (Occupational Safety and Health Administration) requirements. |
Vendor Management |
Manages relationships with equipment vendors, including maintenance contracts, warranty information, and vendor performance evaluations to ensure timely support and optimal service levels. |
Audit Trail |
Maintains a detailed audit trail of all maintenance activities, including changes to equipment configurations, work orders, and maintenance procedures, to support accountability and traceability. |
Training Management |
Tracks technician training and certifications to ensure competency in performing maintenance tasks, schedule training sessions, and maintain documentation for compliance and skill development purposes. |
Condition Monitoring |
Implements condition-based maintenance strategies using sensor data and predictive analytics to monitor equipment health in real-time, enabling proactive maintenance interventions and reducing the risk of failures. |
Asset Lifecycle Management |
Manages the entire lifecycle of manufacturing assets from acquisition to disposal, including asset retirement planning, refurbishment, and replacement strategies to optimize asset performance and minimize total cost of ownership. |
Selecting the Right CMMS for Your Manufacturing Needs
By following these steps, you can effectively select a CMMS that optimizes maintenance operations and supports your manufacturing company’s growth.
- Assess Maintenance Needs: Identify key maintenance requirements such as preventive maintenance, work order management, inventory tracking, etc.
- Research CMMS Solutions: Explore available CMMS options in the market, considering features, compatibility, and user reviews.
- Define Must-Have Features: Determine essential features your CMMS must have to meet your maintenance needs effectively.
- Shortlist Potential Vendors: Narrow down your choices to a select few CMMS providers that align with your requirements and budget.
- Request Demos and Trials: Reach out to shortlisted vendors to request demos or trials of their CMMS software to evaluate usability and functionality.
- Evaluate Support Services: Assess the quality of customer support and training offered by each vendor to ensure smooth implementation and ongoing assistance.
- Check Integration Capability: Ensure that the CMMS can seamlessly integrate with your existing systems, such as ERP software, to streamline processes and data flow.
- Consider Total Cost of Ownership: Evaluate the total cost of ownership, including upfront fees, subscription costs, implementation expenses, and potential additional charges.
- Gather Stakeholder Feedback: Involve relevant stakeholders, such as maintenance staff and management, to gather feedback on the usability and suitability of each CMMS option.
- Make Final Decision: Based on thorough evaluation, stakeholder feedback, and alignment with your company’s needs and budget, select the most suitable CMMS solution for your manufacturing company.
Steps To Successfully Implement A CMMS
After having chosen the CMMS (Computerized Maintenance Management System) of your choice, following are the steps that you must follow to assimilate it in your manufacturing setup.
Step1: Develop an Implementation Plan
Create a detailed implementation plan that includes timelines, milestones, and responsibilities. Ensure the plan is realistic and includes contingencies for potential issues.
Step 2: System Configuration
Configure the CMMS according to your specific requirements. This involves setting up user roles and permissions, defining workflows, and customizing the system to match your processes.
Step 3: Data Migration
Import the collected data into the CMMS. This may involve cleaning and formatting the data to ensure it is compatible with the new system.
Step 4: User Training
Provide comprehensive training for all users, including maintenance staff, managers, and any other stakeholders. Training should cover system navigation, data entry, reporting, and any customized features.
Step 5: Pilot Testing
Deploy the manufacturing maintenance software and conduct a pilot test with a small subset of users or on a specific part of the facility. This helps identify any issues and allows for adjustments before a full-scale rollout.
Step 6: Go Live
After successful pilot testing and addressing any issues, proceed with the full-scale implementation. Ensure all users are informed and supported during the transition.
Step 7: Monitor and Evaluate
Continuously monitor the system’s performance and gather feedback from users. Evaluate whether the CMMS is meeting the defined goals and objectives.
Common Challenges During CMMS Integration
The path to implementation of any enterprise-level application is fraught with many challenges. It applies to integrating a manufacturing CMMS as well. Common challenges that manufacturers encounter in CMMS integration process are:
Data Migration Difficulties
Transferring existing maintenance data to a new CMMS can be problematic due to data inconsistencies, missing information, and differing data structures. You have to have a keen eye on data integrity and accuracy during migration which requires significant effort and expertise. The transition from paper-based logs to a CMMS will involve standardizing maintenance records for equipment like stamping presses and robotic welders, where the chances of containing inconsistent formats and incomplete data is always high.
User Resistance to Change
Employees accustomed to traditional maintenance practices resist adopting a new CMMS due to fear of the unknown or perceived complexity. The resistance is often the reason that slows down implementation and reduces system utilization. The operators and maintenance staff that are used to using manual logs will be reluctant to leverage a CMMS for managing all these activities, fearing that it will complicate their workflow, decrease efficiency, and require them to learn new technical skills.
System Customization Issues
Manufacturing operations often require specific customizations in their CMMS to fit unique workflows, equipment, and processes. These customizations can be technically demanding and time-consuming, leading to potential delays and higher costs. A lack of flexibility in the CMMS can result in a system that doesn’t fully meet the operational needs, impacting efficiency and effectiveness.
Integration with Other Systems
Integrating a CMMS with existing systems like ERP, SCADA, and IoT devices is inherently complex. You have to create interfaces for seamless data exchange, which can be challenging due to differences in data formats, protocols, and security requirements. When you struggle in effectively implementing integration, you fail to synchronize operations and realize the intended benefit with the manufacturing plant maintenance software.
Budget Constraints
Financial incapability can force compromises, such as opting for a less robust system, going for in-house training, or limiting the scope of implementation. Financial limitations will always hinder the full realization of the CMMS benefits, and lead to suboptimal performance and don’t offer any return on investment (ROI).
Trends Unfolding in Manufacturing CMMS
Artificial Intelligence (AI) capabilities are becoming common in modern maintenance management systems. Also, CMMS is now a part of the IoT ecosystem as manufacturers have moved to the industry 4.0 landscape. In the coming days, we can expect the following trends to become part of the CMMS ecosystem:
Edge Computing Integration
With the help of edge computing, CMMS systems will experience reduction in latency in data processing and communication, and ensure quicker response times for maintenance alerts, diagnostics, and actions.
AR and VR assisted Maintenance
Integrate augmented reality (AR) and virtual reality (VR), a CMMS software for manufacturing will provide technicians with augmented views of equipment overlaid with digital information such as maintenance instructions, schematics, and real-time equipment data.
Human-Robot Collaboration
CMMS systems will work with collaborative robots (cobots) such as cameras and sensors, integrating them with existing CMMS platforms to perform routine maintenance tasks alongside human technicians.
Voice-Activated Interfaces
Equipped with advanced NLP technologies, CMMS will offer interfaces that will help in accurately interpreting and processing voice commands from technicians. The capability will improve the process to retrieve instructions or manuals without having to manually input information or use touchscreen interfaces.
Sustainability and Circular Economy Practices
You will find a good maintenance management system supporting the implementation of sustainable maintenance strategies by providing analytics and insights into energy consumption, carbon emissions, and environmental impact. There will be an increased focus on sustainability features in the coming days.
Conclusion
Implementing a CMMS has to be a priority for all manufacturers who are keen on optimally managing their maintenance function. A CMMS empowers manufacturers to meet production targets effectively and promotes a culture of innovation and competitiveness, thereby positioning manufacturing enterprises for sustainable growth in the market.
FieldCircle offers the best CMMS software for manufacturing, built keeping in mind the divergent needs of manufacturing organizations. Reach out to us to know how it will generate value for you.