A Detailed Welding Machine Preventive Maintenance Checklist
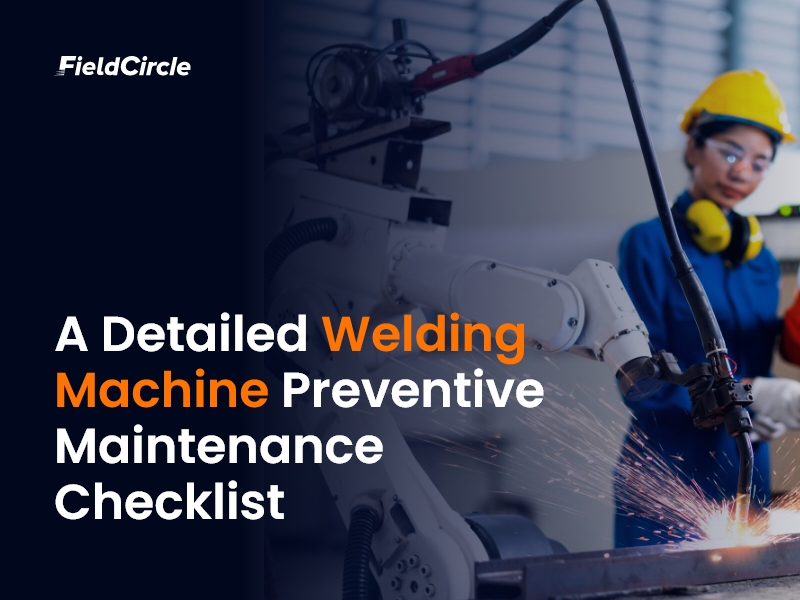
Used across a range of industries, welding machines are exposed to tough conditions—metal dust, heat cycles, voltage fluctuations, and mechanical strain. These factors gradually wear down components – many times – without immediate warning. When issues surface during production, they compromise weld quality and welder safety.
When you think about welding machine maintenance, you have to think about several elements. Because, from checking cables for insulation cracks to clearing blocked vents or recalibrating voltage settings, every task has a direct impact on machine reliability. Here, you need a comprehensive preventive maintenance checklist for welding machines.
In the sections ahead, we break down a detailed, field-tested checklist designed for daily, weekly, and long-term maintenance of your welding machines which will help you to keep the performance of your welding machine steady.
What is a Welding Machine Preventive Maintenance Checklist?
A welding machine preventive maintenance checklist is a structured document that outlines routine maintenance and inspection actions tailored to the machine’s operating demands. It covers activities such as examining connections, clearing internal dust, testing outputs, and inspecting consumables to keep the unit electrically stable, thermally safe, and mechanically sound across repeated welding cycles without drifting into performance loss or unexpected shutdowns.
What are the Benefits of a Welding Machine Preventive Maintenance Checklist?
Regular use of a preventive maintenance checklist does more than keep equipment functional—it adds value across operations, safety, and long-term asset performance, and offers many benefits like:
- Early Detection of Functional Issues
A checklist directs attention to wear indicators and operational anomalies, allowing technicians to catch faults before they interrupt welding cycles or compromise output quality.
- Reduced Unscheduled Downtime
Following a structured maintenance routine helps avoid unexpected machine halts, keeping fabrication schedules intact and production floor activity uninterrupted.
- Consistent Weld Quality
Frequent monitoring of settings and components stabilizes weld parameters, reducing chances of defects such as porosity, undercut, or poor fusion.
- Protection of Internal Components
Replacing degraded parts as per the checklist protects surrounding components from cascading failures, limiting the extent and cost of necessary repairs.
- Greater Operational Accountability
A welding machine inspection checklist provides a documented record of maintenance activity, making it easier to trace oversights, missed steps, or recurring mechanical issues.
- Longer Equipment Lifespan
Routine inspections help preserve machine integrity by preventing buildup, overheating, and electrical strain—factors that shorten service life over time.
Welding Machine Maintenance Checklist
Following are the highly critical 11 items that your checklist for preventive maintenance of welding machines must have:
1. Welding Torch and Gun
- Torch Condition
- Check the MIG gun body (torch) for cracks, dents, or discoloration.
- Inspect the MIG gun cable for fraying, cuts, or wear.
- Ensure all electrical connections on the MIG gun are secure and tightly fastened.
-
Clean the MIG gun to remove dirt, debris, or slag buildup.
- Nozzles and Contact Tips
- Check the MIG gun nozzle for cracks, excessive wear, or signs of overheating. Replace if needed.
- Remove welding spatter or residue from the MIG gun nozzle.
- Ensure MIG gun contact tips are free from cracks, corrosion, or wear. Replace if necessary.
-
Make sure the MIG gun contact tip is properly seated and securely tightened.
- Electrode Holder
- Check the electrode holder for cracks or broken parts.
- Inspect the insulation for wear or damage.
- Ensure the electrode holder is tightly connected to the welding cable.
-
Clean the electrode holder to remove welding spatter, dirt, or slag.
2. Cooling System
- Inspect Cooling System for Leaks
- Check all hoses, fittings, and connectors for visible signs of leakage.
- Look for any wet spots around the connections that might indicate a slow leak.
-
Tighten or replace any loose or damaged connections to prevent coolant leakage.
- Verify Coolant Flow
- Ensure that coolant flows freely through the cooling system and the torch (for water-cooled systems).
- Test the coolant pump to ensure it is operating at the correct pressure and flow rate.
-
Check that no kinks or blockages are obstructing the coolant lines.
- Check Coolant Level
- Inspect the coolant reservoir to ensure the coolant level is within the recommended range.
- Refill the coolant if the level is low, using the appropriate type as specified by the manufacturer.
-
Make sure the coolant is not contaminated or dirty. Replace if necessary.
- Inspect Cooling Fans (Air-Cooled Systems)
- Check that the cooling fans are functioning properly.
- Clean any dust or debris from the fan blades and vents.
-
Ensure the fan motor runs smoothly and the fan blades rotate freely without obstruction.
- Clean Cooling System Components
- Remove any dirt, debris, or residue from the cooling lines and coolant reservoir.
-
Flush the cooling system periodically to remove any contaminants or buildup that could obstruct the flow.
- Inspect Heat Exchanger (If Applicable)
- Check the heat exchanger for any signs of wear or corrosion.
- Clean the heat exchanger fins to ensure efficient heat dissipation.
-
Inspect the heat exchanger connections for tightness and any potential leaks.
3. Gas Supply System
- Inspect Gas Hoses
- Check the gas hoses for cracks, cuts, or signs of wear that could lead to leaks.
- Ensure the hoses are free from kinks or bends that may restrict gas flow.
-
Replace any damaged or worn hoses immediately.
- Test for Gas Leaks
- Perform a leak test by applying soapy water to all gas connections, valves, and regulators.
- Look for bubbles forming around connections, indicating a gas leak.
-
Tighten any loose connections or replace faulty components to stop leaks.
- Verify Gas Pressure
- Check the pressure setting on the gas regulator to ensure it matches the recommended operating pressure for the welding process.
- Test the gas flow with a flowmeter to confirm that the flow rate is within the specified range.
-
Adjust the regulator if necessary to maintain the correct pressure.
- Inspect Gas Regulators
- Check the gas regulators for signs of damage or wear.
- Test the regulator functionality by turning it on and off to ensure it maintains consistent pressure.
-
Ensure the regulator’s valve operates smoothly and is free from obstructions or leaks.
- Inspect Gas Cylinders
- Check the gas cylinders for proper labeling, certification, and expiration dates.
- Ensure the cylinder valve is tightly closed when not in use.
-
Inspect the cylinder’s condition for dents, rust, or damage that may compromise its integrity.
- Ensure Proper Ventilation
- Ensure that the area around the gas cylinders is well-ventilated to prevent the buildup of hazardous gases.
-
Verify that no gas supply hoses are positioned in a way that could be accidentally stepped on, crushed, or obstructed.
- Clean Gas Lines and Filters
- Regularly clean the gas lines and filters to remove any dirt, moisture, or contaminants that could affect gas quality.
- Replace gas filters if they are clogged or appear worn out.
4. Drive System
- Inspect Wire Feed Mechanism
- Check the wire feeder motor for proper functioning and ensure it operates without hesitation.
- Inspect the wire feeder rollers for signs of wear, grooves, or damage.
- Clean the rollers to remove any built-up wire residue or debris that could affect feeding accuracy.
- Verify that the wire is feeding smoothly and consistently without binding or skipping.
-
Inspect the wire liner for blockages, excessive wear, or kinks.
- Test Wire Speed Control
- Check the wire speed control settings to ensure they are functioning correctly.
- Test the wire speed at different settings to confirm that it adjusts smoothly without fluctuations.
-
Inspect the potentiometer or control knob for wear or malfunction.
- Check Tension Settings
- Inspect the wire feed tension and adjust as needed to ensure the correct level of pressure is applied to the wire.
- Test the wire feed under tension to make sure the wire feeds smoothly through the system without slipping or overfeeding.
-
Adjust the tension on the wire feed rollers based on the type of wire being used and the welding requirements.
- Inspect and Clean Drive Rolls
- Inspect the drive rolls for wear, cracks, or grooves. Replace them if necessary.
- Ensure that the drive rolls are properly aligned with the wire and that they rotate smoothly.
-
Clean the drive rolls to remove any spatter or contaminants that could affect wire feeding.
- Verify Wire Spool Condition
- Inspect the wire spool for proper placement and ensure it rotates freely without obstruction.
- Check the spool for any signs of damage, such as bent or broken parts.
-
Ensure the wire spool is not overloaded, and verify the correct wire diameter is used.
- Inspect and Clean Feed Path
- Inspect the wire feed path for any obstacles, misalignments, or debris that may cause the wire to become jammed.
- Clean the feed path to remove any debris, dirt, or contaminants that could interfere with smooth wire feeding.
-
Ensure all guides and rollers are correctly positioned and aligned to avoid excessive friction.
- Test Drive System Performance
- Test the overall performance of the drive system by feeding wire through the torch and ensuring a consistent, smooth feed.
- Check for any irregularities such as slipping, binding, or inconsistent feeding and address them immediately.
- Adjust the system settings to achieve optimal wire feed performance for various welding tasks.
5. Machine Bed and Frame
- Inspect the Machine Frame for Damage
- Check the machine frame for any cracks, dents, or other signs of physical damage that could affect its structural integrity.
- Look for signs of stress or bending in critical areas of the frame, particularly around mounting points or where the machine bears weight.
-
Ensure the frame is properly aligned and has not shifted out of place due to wear or external forces.
- Verify Proper Alignment
- Check the alignment of all key machine components, ensuring they are positioned correctly relative to each other.
- Use precision tools (e.g., a laser level or dial indicator) to verify the straightness of the machine bed.
-
Adjust any misaligned parts to ensure smooth operation and reduce strain on moving components.
- Inspect Mounting Points and Bolts
- Check all mounting bolts and screws for tightness to prevent movement or loosening during operation.
- Inspect bolts for signs of wear or corrosion, and replace them if necessary.
-
Tighten any loose mounting points to ensure that the machine remains stable during operation.
- Check for Rust or Corrosion
- Inspect the entire machine bed and frame for signs of rust or corrosion, particularly in areas exposed to moisture or coolant.
- Clean and treat any rusted or corroded areas with appropriate cleaning agents and rust inhibitors.
-
Apply a protective coating to prevent future rust buildup.
- Clean the Machine Bed
- Clean the machine bed thoroughly to remove dirt, dust, and any metal debris that may have accumulated.
- Use a soft cloth or brush to avoid scratching or damaging the surface.
-
Ensure the surface is smooth and free from foreign objects that could interfere with machine operation.
- Inspect Vibration Dampening
- Check the vibration dampening system (if equipped) to ensure it is functioning properly.
- Inspect shock absorbers or vibration isolators for any signs of wear or damage.
-
Replace worn or damaged vibration dampening components to reduce machine vibration and prevent wear on the drive system.
- Check for Movement or Shifting
- Test the machine bed for any signs of excessive movement or shifting during operation.
- Ensure the machine is securely bolted to its foundation or support structure.
- Tighten any mounting hardware that may have loosened over time.
6. Welding Wire and Consumables
- Inspect Welding Wire
- Check the welding wire spool for any signs of damage or contamination, such as rust or moisture.
- Ensure the wire is correctly wound and not tangled or bent, which can affect its feeding and performance.
- Verify the wire diameter to ensure it matches the specifications for the welding task.
-
Check the wire surface for any irregularities, such as flattening, which could cause feeding problems.
- Check Wire Spool Condition
- Inspect the spool for any cracks, dents, or deformations that could prevent smooth rotation during use.
- Ensure the spool is securely mounted and rotates freely without wobbling or binding.
-
Check that the spool is not overloaded and that the wire is not under excessive tension during feeding.
- Clean the Welding Wire
- Clean the wire if it has been exposed to dust, dirt, or other contaminants, which can affect welding quality.
- Use a clean, dry cloth to wipe down the wire and remove any foreign particles.
-
If necessary, use a specialized wire cleaning solution to remove oil, grease, or rust.
- Inspect Other Consumables
- Check electrodes and welding rods for cracks, moisture absorption, or damage.
- Ensure consumables are stored in appropriate conditions (e.g., dry environment for rods to prevent moisture absorption).
-
Verify that the consumable size matches the specifications for the welding process and material type.
- Verify Proper Storage of Consumables
- Ensure that consumables are stored in a dry, clean, and well-organized manner to prevent contamination or damage.
- Check that electrodes, rods, and other consumables are stored in their designated packaging or containers to maintain their quality.
-
Rotate stock to ensure older consumables are used first, preventing expired or degraded materials from being used.
- Inspect Gas Nozzles and Tips
- Check gas nozzles for any signs of wear, cracks, or clogging.
- Ensure the gas tips are clean and free of welding spatter or other residues that can restrict gas flow.
-
Verify that nozzles are properly seated and tightened on the torch.
- Check Spatter Shield and Diffuser
- Inspect spatter shields for wear, corrosion, or damage that could affect shielding gas flow or welding quality.
- Clean or replace the spatter shield as needed to maintain optimal shielding during welding.
-
Ensure the diffuser is correctly installed and free from debris that could obstruct the gas flow.
7. Control Panel and Electronics
- Inspect Control Panel for Physical Damage
- Check the control panel for any cracks, dents, or visible signs of damage.
- Ensure all buttons, switches, and dials are intact and operate smoothly without sticking or malfunctioning.
-
Inspect the control panel faceplate for cleanliness and ensure it’s free from dirt, grease, or residue.
- Test All Buttons, Knobs, and Switches
- Test each button, knob, and switch on the control panel to ensure proper functionality.
- Verify that the switches click or engage smoothly and that there’s no resistance or “jamming.”
-
Ensure that the functions associated with each button or dial (e.g., wire speed, voltage, amperage) respond accurately.
- Check Display Screens and Meters
- Inspect any digital or analog displays on the control panel for readability and accuracy.
- Verify that the readouts for parameters such as voltage, amperage, and wire speed are correct and correspond to the machine settings.
- Ensure that the display screens or meters are not cracked or malfunctioning.
-
Perform a calibration check, if required, to ensure the meters show correct readings.
- Inspect Circuit Boards and Connections
- Open the control panel and check the circuit boards for visible signs of wear, corrosion, or loose components.
- Inspect the connections for any signs of overheating, such as discolored terminals or melted plastic.
-
Ensure that all wires are properly connected, and no loose or exposed wires are present.
- Test Electronics and Sensors
- Check all electronic components, such as sensors and relays, to verify they are functioning properly.
- Test the weld output response from the control panel to ensure that adjustments to settings (voltage, amperage, wire speed) result in corresponding changes in performance.
-
Inspect and test safety sensors, such as thermal overload or gas flow sensors, to verify they are working properly.
- Clean Control Panel and Electronics
- Clean the control panel with a soft, dry cloth to remove any dust, dirt, or debris.
- Use compressed air to blow out any dust or particles inside the control panel, being cautious not to damage sensitive components.
-
Avoid using liquid cleaners directly on the control panel or electronics.
- Update Software/Firmware
- If the machine uses software or firmware for operation, check for any available updates from the manufacturer.
- Follow the manufacturer’s guidelines to update the system if necessary, ensuring the machine operates with the latest software features and security improvements.
- Perform a system reset after updates to ensure proper functioning of all software-related features.
8. Electrical System
- Power Supply
- Check for any wear or damage on the power supply cables and connectors.
- Inspect the power cable insulation for cracks or fraying.
-
Ensure that power cables are properly secured to prevent excessive movement.
- Grounding System
- Check the grounding wire for corrosion or physical damage.
- Ensure the grounding connections are tight and free of rust.
-
Verify that the grounding system is effectively connected to the welding machine frame.
- Circuit Breakers/Fuses
- Inspect circuit breakers and fuses for signs of overheating, wear, or burn marks.
- Test each breaker by manually tripping them to ensure they reset properly.
-
Replace any damaged fuses or reset circuit breakers if tripped.
- Electrical Connections
- Tighten any loose connections between electrical components, such as the power supply terminals and internal wiring.
- Inspect electrical connectors for corrosion or dirt and clean them if necessary.
-
Test continuity of important electrical paths (e.g., power to control panel) using a multimeter.
- Voltage Settings
- Test the welding machine’s input voltage and ensure it matches the specified requirements.
- Adjust the voltage settings on the control panel, and verify they correspond to the desired output.
-
Ensure proper calibration of the voltage adjustment knobs for accurate welding output.
9. Temperature and Humidity Control
- Temperature Sensors
- Inspect temperature sensors for proper installation and secure mounting.
- Test the sensors with a calibrated thermometer to verify their accuracy.
-
Replace faulty or damaged temperature sensors that do not give consistent readings.
- Cooling System
- Verify that the cooling system is maintaining an appropriate temperature by checking coolant levels and circulation.
- Inspect water-cooled systems for leaks, and ensure that coolant flows freely without obstruction.
-
Ensure air-cooled systems have proper airflow to maintain safe operating temperatures.
- Thermostat/Temperature Control
- Verify that the thermostat or temperature control unit is functioning accurately and is set to the correct temperature range.
- Test the system under load to ensure that it can maintain the set temperature during operation.
- Adjust the thermostat as needed if the temperature readings fluctuate beyond acceptable limits.
10. Calibration and Accuracy
- Voltage and Amperage Settings
- Test the voltage and amperage output of the welding machine using a multimeter or weld meter to ensure it matches the settings.
- Compare actual output readings to the desired welding parameters and adjust if necessary.
-
Calibrate the voltage and amperage controls to ensure consistency in output.
- Wire Feed Speed
- Check that the wire feed speed is consistent with the settings on the control panel.
- Verify the wire feed is smooth, and there is no binding or skipping during operation.
-
Adjust the wire feed settings as needed to maintain accuracy in feeding and welding results.
- Alignment and Geometry
- Check the alignment of the welding torch, wire feed mechanism, and machine bed to ensure that they are properly aligned for effective welding.
- Use precision tools to ensure the wire and torch are correctly positioned relative to the workpiece.
-
Calibrate the machine to correct any misalignment that could affect the quality of the weld.
- Perform Test Welds
- Conduct test welds to verify the machine’s performance and the accuracy of the settings.
- Assess the weld quality for consistency, penetration, and appearance.
- Adjust settings as necessary based on the results of test welds.
11. Safety Features and Systems
- Test Emergency Stop Function
- Test the emergency stop button and ensure it halts the machine immediately without delay.
- Inspect the wiring and connections to the emergency stop system for any damage or loose connections.
-
Ensure that the emergency stop feature is accessible and clearly marked for quick use during an emergency.
- Inspect Safety Interlocks
- Check all safety interlocks to ensure they prevent operation in unsafe conditions (e.g., when a door or cover is open).
- Verify that safety covers, shields, and doors are securely fastened and prevent access to dangerous components while operating.
-
Test the interlock system to confirm that it prevents the machine from running if safety conditions are not met.
- Check Overload Protection
- Ensure the overload protection system is properly calibrated and responds when the machine exceeds its maximum rated capacity.
- Test the machine under load conditions to verify that the protection system activates to prevent overheating or damage.
-
Inspect thermal protection sensors to ensure they are functioning correctly and shut down the machine when overheating occurs.
- Inspect Fire Safety Systems
- Check that fire extinguishers are in place, properly charged, and easily accessible near the welding area.
- Inspect fire blankets and other fire safety equipment for wear or damage.
-
Ensure that the machine’s fire suppression systems (if equipped) are operational and properly maintained.
- Verify Welding Shielding
- Inspect the welding shield to ensure it is free from cracks or signs of wear.
- Ensure that the shield provides adequate protection from UV radiation and welding fumes.
-
Check the clarity of the viewing lens and replace it if it’s damaged or too cloudy.
- Check Electrical Insulation
- Inspect all exposed electrical components, wires, and connections to ensure they are properly insulated.
- Ensure that no wires or electrical parts are exposed to moisture, heat, or debris that could lead to short circuits.
- Check for any exposed terminals or faulty insulation that could present an electrical hazard to operators.
What are the Tips to Follow for a Welding Machine Preventive Maintenance Checklist?
Following are key maintenance tips that support the dependable functioning of welding machines and keep performance steady across various operating conditions:
- Check Power Connections
Inspect all terminals and cable ends for tightness and signs of corrosion or burns; replace connectors that show wear or discoloration.
- Clean Vents and Fans
Clear dust from vents and confirm the fan blades rotate freely; blocked airflow leads to internal heat buildup and shortens equipment life.
- Inspect Cables and Hoses
Look for cuts, cracks, or exposed conductors in cables and hoses; replace damaged parts immediately to avoid arc instability or gas leakage.
- Test Output Levels
Use a multimeter to match the machine’s output with the manufacturer’s ratings; any mismatch indicates calibration or internal component faults.
- Examine Ground Connections
Check that the ground clamp contacts clean metal and that the ground cable shows no signs of fraying or overheating.
- Verify Safety Mechanisms
Test emergency stop functions, thermal cutoffs, and insulation strength regularly; faulty safety features create serious risks during operation.
To Wrap Up
Preventive maintenance of welding machines is a key part of industrial maintenance activities. It may seem routine, but without a defined checklist, even the most experienced operators can overlook essential steps.
A checklist brings order, accountability, and repeatability to the process—turning scattered efforts into a systematic approach. More than just a list, it reflects a commitment to machine care and operational discipline. Whether used daily, weekly, or monthly, it sets the tone for how welding equipment should be handled—proactively, not reactively.
Download our welding machine maintenance checklist to experience smooth sailing in your maintenance operations. It will prove to be a great lever to build a highly effective preventative maintenance program for your welding equipment.