A Detailed Equipment Preventive Maintenance Checklist
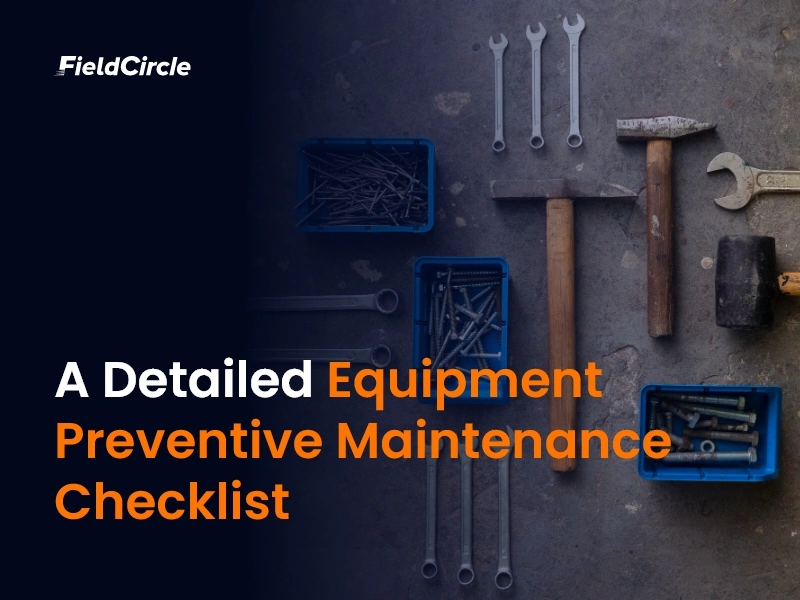
Equipment keeps the engines of industries running — whether it’s construction, manufacturing, agriculture, or warehousing. From heavy-duty machinery to specialized production units, equipment is essential for maintaining smooth operations and meeting project deadlines.
The efficiency and reliability of equipment are governed by a strong preventive maintenance program. It directly affects the performance of operators, the safety of work environments, and the overall project timelines. At the heart of a well-run maintenance process lies a comprehensive checklist that keeps maintenance efforts organized and systematic.
While the maintenance needs of different equipment can vary based on their design and usage, there are core areas common to all types. To address both universal and specialized maintenance needs, we have developed a complete generic checklist that applies across equipment categories, along with specialized lists tailored for specific equipment types and industries, and is useful for maintenance team members and all maintenance stakeholders. Before diving into the checklists, let’s first understand what an equipment maintenance checklist actually means and the key benefits it offers.
What is an Equipment Preventive Maintenance Checklist?
An equipment preventive maintenance checklist is a structured tool designed to organize, monitor, and execute routine maintenance tasks for different machinery. It provides detailed guidance on inspections and actions related to critical components such as hydraulic systems, electrical connections, fluid levels, safety mechanisms, and moving parts — keeping equipment functioning safely and efficiently.
What are the Benefits of an Equipment Preventive Maintenance Checklist?
A preventive maintenance (PM) checklist for equipment brings a structured, disciplined approach to keeping machinery in peak operating condition. It offers several critical advantages:
-
Improved Equipment Reliability
Regular inspections and servicing keep equipment running consistently without unexpected failures. Over time, these actions boost operational reliability, minimize disruptions, and maintain production or project timelines without costly interruptions. -
Increased Equipment Lifespan
Well-maintained equipment experiences less wear and tear over time. A preventive maintenance checklist helps extend the operational life of machines, delaying the need for expensive replacements and maximizing return on investment. -
Reduced Risk of Major Failures
Preventive maintenance helps detect early signs of wear, fatigue, or damage in mechanical, electrical, and hydraulic systems. Addressing small issues before they escalate drastically reduces the risk of sudden, catastrophic equipment failures. -
Improved Operator Safety
Faulty equipment can be dangerous for operators and nearby workers. A proper maintenance checklist ensures that safety-critical components like brakes, sensors, emergency shut-offs, and protective guards are functioning properly, reducing the risk of workplace accidents. -
Optimized Equipment Performance
Routine maintenance like lubrication, filter replacement, calibration, and fluid checks keeps equipment operating at optimal levels. Machines deliver better output, improved energy efficiency, and smoother operation when maintained systematically. -
Regulatory Compliance
Many industries are subject to strict maintenance and safety regulations (e.g., OSHA, MSHA). A preventive maintenance checklist helps organizations stay compliant by documenting inspections, repairs, and part replacements, avoiding fines and legal complications. -
Lower Overall Maintenance Costs
Proactive maintenance cuts down on emergency repairs, overtime labor charges, and unnecessary part replacements, thereby automatically bringing down maintenance costs. By preventing major breakdowns, maintenance budgets become more predictable, and unplanned expenses are significantly reduced. -
Streamlined Workflows and Scheduling
A checklist makes it easier to schedule maintenance around project timelines without unexpected delays. With an equipment preventive maintenance plan in your hand, you can methodically perform the maintenance process, reduce downtime, and thus ensure minimum disruption to operational activities.
Equipment Preventive Maintenance Checklist
An equipment preventive maintenance checklist comprises the following 10 parts. Understand and learn what each part comprises:
1. Mechanical Components
- Engines and Motors:
-
Check oil levels and quality.
-
Inspect belts, hoses, and pulleys for wear or cracks.
-
Ensure proper lubrication on moving parts (motors, gears, etc.).
-
Inspect air filters for cleanliness; replace if clogged.
-
Check for abnormal noise, overheating, or vibration.
-
Check for proper alignment and test operation under load.
-
Inspect spark plugs (if applicable) and replace if worn.
- Pumps, Compressors, and Fans:
-
Inspect seals and gaskets for leaks or wear.
-
Check belt tension, alignment, and adjust if necessary.
-
Test operation of pressure relief valves.
-
Verify motor function and check for overheating.
-
Inspect for excessive vibration or noise.
-
Check fluid levels in pumps and motors.
-
Inspect and clean cooling fans and fan blades.
- Bearings and Gearboxes:
-
Check bearings for wear and replace as needed.
-
Monitor lubrication levels and top up or change oil as needed.
-
Inspect gearboxes for leaks or signs of wear.
-
Inspect for unusual noise or overheating.
-
Verify correct alignment and adjust as necessary.
-
Clean and lubricate any exposed gear and bearing parts.
- Hydraulic Systems:
-
Check hydraulic fluid levels and top up if necessary.
-
Inspect hydraulic hoses for signs of wear, cracks, or leaks.
-
Test pressure relief valves and ensure they are functioning properly.
-
Clean hydraulic filters or replace if necessary.
-
Inspect hydraulic pumps and motors for signs of wear.
-
Test system for pressure and fluid contamination.
- Structural Components:
-
Inspect equipment for cracks, corrosion, or other structural issues.
-
Examine fasteners, bolts, and welds for stress or fatigue.
-
Inspect load-bearing parts for wear, bending, or fatigue.
-
Verify the integrity of support structures and frames.
-
Apply anti-corrosion treatments if needed.
2. Electrical Systems
- Wiring and Cables:
-
Inspect cables for fraying, cuts, or damage.
-
Check for signs of overheating, discoloration, or burning.
-
Tighten and secure all loose connections.
-
Test insulation resistance and ensure proper grounding.
-
Replace worn or damaged cables.
-
Verify proper voltage and current flow.
- Batteries:
-
Check charge levels and replace batteries nearing end of life.
-
Clean terminals and ensure there is no corrosion.
-
Inspect battery housing for cracks, leaks, or damage.
-
Verify the proper operation of battery backup systems.
-
Test battery voltage and compare with manufacturer specifications.
-
Ensure batteries are securely mounted and connections are tight.
- Control Panels:
-
Test functionality of all control switches, buttons, and relays.
-
Inspect for overheating (check for discoloration, burning).
-
Ensure proper grounding of control panels.
-
Replace blown fuses or tripped circuit breakers.
-
Clean dust or debris from control panel components.
-
Verify operation of indicators and alarms.
- Motors and Circuit Breakers:
-
Test for proper function of motor protection devices (e.g., overload relays).
-
Inspect for overheating or tripping of circuit breakers.
-
Verify proper voltage and current values.
-
Clean terminals and check connections for corrosion or looseness.
-
Inspect for any signs of wear or malfunction in the motor windings.
-
Perform operational tests under load.
- Lighting Systems:
-
Test all lights for functionality and replace any burnt-out bulbs.
-
Check for proper voltage and ensure the electrical circuit is stable.
-
Inspect wiring and fixtures for wear or damage.
-
Clean light covers and lenses for optimal brightness.
-
Ensure emergency lighting is operational.
-
Inspect switches and dimmers for correct operation.
3. Safety and Emergency Systems
- Fire Protection Equipment:
-
Inspect fire extinguishers for proper charge and expiration date.
-
Check fire alarms and test for proper activation.
-
Inspect sprinkler systems for blockages or leaks.
-
Test emergency lighting for proper function.
-
Ensure fire exit doors are unobstructed and functional.
-
Verify fire detection systems (smoke detectors, heat sensors) are operational.
- Emergency Shut-Off Valves:
-
Test all emergency shut-off valves to ensure they activate quickly.
-
Inspect for leaks around valve seals and connections.
-
Verify valve operation during a pressure test.
-
Lubricate shut-off valves to prevent sticking or malfunction.
-
Ensure valve labels are visible and instructions are clear.
-
Check for any signs of corrosion on valve components.
- Safety Guards and Shields:
-
Inspect safety guards for physical damage, cracks, or wear.
-
Ensure guards are properly aligned and fixed in place.
-
Test emergency stop functions for effectiveness.
-
Verify the presence of appropriate signage and safety labels.
-
Check for any exposed moving parts that may pose a risk.
- First-Aid Kits and Emergency Supplies:
-
Verify the contents of first-aid kits are up to date.
-
Replace any expired medications or bandages.
-
Inspect emergency eyewash stations and replenish fluids.
-
Check defibrillator battery charge (if applicable).
-
Ensure all emergency supplies are easily accessible.
- Verify the availability of fire blankets, eye wash, and other safety supplies.
4. Cooling and Heating Systems
- Air Conditioning Units:
-
Inspect air filters for cleanliness and replace if clogged or dirty.
-
Check refrigerant levels and top up if necessary.
-
Clean condenser and evaporator coils to remove dirt and dust buildup.
-
Inspect fans for proper operation and vibration.
-
Test airflow to ensure the unit is cooling effectively.
-
Inspect ductwork for leaks or blockages.
-
Check thermostat settings and verify temperature accuracy.
-
Inspect insulation on refrigerant lines and replace if damaged.
-
Test system for unusual noises or odors.
- Heaters and Boilers:
-
Inspect pressure relief valves for correct operation.
-
Check and flush the heating system to remove sediment buildup.
-
Inspect and clean burner components.
-
Verify proper functioning of ignition systems.
-
Test operation of the thermostat and calibration.
-
Inspect all piping for leaks or corrosion.
-
Check fluid levels in heating systems and top up as necessary.
-
Test boiler combustion levels and check for soot buildup.
-
Verify ventilation and exhaust systems are clear of blockages.
-
Inspect pressure gauges and ensure accurate readings.
- Ventilation Systems:
-
Clean ducts and ensure proper airflow.
-
Inspect filters and replace if dirty or clogged.
-
Test all ventilation fans for proper functioning.
-
Inspect and clean dampers and louvers for smooth operation.
-
Check the motor and bearings for wear or unusual noise.
-
Test the system for air leaks and seal any gaps.
-
Inspect vents and exhausts to prevent buildup of debris.
-
Ensure that the airflow meets operational standards.
-
Inspect exhaust systems for carbon monoxide buildup or clogs.
5. Lubrication Systems
- Oil and Grease:
-
Check oil levels in all moving parts, such as gears, bearings, and pumps.
-
Ensure oil is clean and free from contaminants.
-
Change oil in engines, compressors, and hydraulic systems if necessary.
-
Lubricate bearings, gearboxes, and moving components as per manufacturer guidelines.
-
Ensure that grease fittings are working and clean any excess grease.
-
Inspect oil seals and gaskets for leaks.
-
Test for excessive noise or vibration in lubricated components.
-
Check fluid viscosity to make sure it meets operating conditions.
-
Dispose of used lubricants in an environmentally friendly manner.
- Automated Lubricators:
-
Test automated lubrication systems for proper operation.
-
Inspect lubrication lines for wear, leaks, or blockages.
-
Replenish lubrication fluid in automated systems as necessary.
-
Check filters and strainers for contamination.
-
Calibrate automatic lubricators according to manufacturer specifications.
- Check for any malfunctions or irregularities in automated delivery systems.
6. Fluid Systems
- Fuel Systems:
-
Check fuel quality and replace if contaminated (e.g., water, debris, algae).
-
Inspect fuel lines for cracks, leaks, or signs of wear.
-
Test fuel pressure and verify proper fuel flow.
-
Clean or replace fuel filters as necessary.
-
Check for airlocks in the fuel system and bleed if required.
-
Inspect fuel tank for rust, corrosion, or sludge buildup.
-
Test the fuel injector systems and verify proper function.
-
Ensure proper sealing of fuel tanks and connections.
- Hydraulic Fluids:
-
Inspect hydraulic fluid levels and top up with the correct fluid type.
-
Replace contaminated hydraulic fluid if necessary.
-
Clean or replace hydraulic filters as required.
-
Inspect hydraulic hoses for wear, cracking, or leaks.
-
Test hydraulic system pressure and verify that it meets operational standards.
-
Inspect hydraulic cylinders for fluid leakage and damage.
-
Lubricate hydraulic components such as valves, seals, and actuators.
- Cooling Fluids:
-
Check coolant levels and top up with appropriate coolant fluid.
-
Inspect coolant lines for leaks, cracks, or damage.
-
Test radiator cap for proper sealing and pressure retention.
-
Inspect heat exchangers for signs of wear or blockage.
-
Check for sediment or sludge buildup in the cooling system.
-
Replace coolant fluid if it is degraded or contaminated.
-
Test the system for overheating and ensure proper flow through the radiator.
7. Calibration and Measurement Equipment
- Instruments:
-
Inspect instruments for visible damage or wear.
-
Check calibration against known standards or master gauges.
-
Calibrate instruments as per operational standards.
-
Test instruments for accuracy of readings.
-
Ensure gauges and meters are functional and provide correct readings.
-
Inspect power sources (batteries or mains) for reliability.
-
Perform operational tests under controlled conditions.
-
Record calibration results for future reference.
- Sensors and Gauges:
-
Inspect sensors for proper mounting and alignment.
-
Verify that sensors are properly calibrated and provide accurate readings.
-
Test sensors for proper response time and accuracy.
-
Clean sensors and replace protective covers if needed.
-
Inspect wiring and connections for wear, loose connections, or damage.
-
Verify the condition and function of temperature, pressure, and flow gauges.
-
Test signal output from sensors to ensure it matches expected values.
8. Environmental Control Systems
- Water Treatment Systems:
-
Inspect water filters for debris and replace them if necessary.
-
Test water hardness and pH levels, and adjust treatment as required.
-
Check for leaks in water pipes and connections.
-
Inspect water pumps for proper operation and seal integrity.
-
Clean or replace any clogged filters or strainers.
-
Verify correct chemical dosing (chlorine, pH adjusters, etc.).
-
Inspect backflow prevention devices for function and leaks.
-
Test system for potential contamination or microbial growth.
-
Check water tanks for corrosion, scale buildup, or debris.
- Wastewater Systems:
-
Inspect waste treatment tanks and ensure there is no overflow or leakage.
-
Check pumps and valves for proper operation.
-
Test for blockages in sewage lines and clear if necessary.
-
Inspect filtration systems for clogging or wear.
-
Verify proper ventilation to prevent odor buildup.
-
Check aeration systems for efficiency and proper oxygen levels.
-
Inspect backup pumps and power systems for readiness.
-
Verify the accuracy of wastewater metering and monitoring equipment.
- Air Quality Control:
-
Check air filters in HVAC and ventilation systems for cleanliness.
-
Test air quality sensors for proper function (e.g., CO2, CO, particulate matter).
-
Inspect exhaust systems to ensure proper air filtration.
-
Check for proper operation of air scrubbers and purifiers.
-
Inspect air dampers and ensure they open/close properly.
-
Verify that all ventilation fans are working and free from blockages.
-
Inspect humidity control systems and test for correct operation.
-
Clean air ducts and ensure no blockages are present.
9. Transport and Conveyor Systems
- Conveyor Belts:
-
Inspect belts for signs of wear, fraying, or tears.
-
Check belt tension and adjust if necessary.
-
Inspect rollers and pulleys for damage or excessive wear.
-
Test for smooth operation and check for noise or vibration.
-
Lubricate rollers and moving parts to ensure smooth operation.
-
Clean the conveyor system to remove debris and dirt buildup.
-
Test emergency stop functions and other safety mechanisms.
-
Inspect drive motors for proper operation and check for overheating.
- Trucks, Forklifts, and Material Handling Equipment:
-
Inspect fuel levels and check for any leaks.
-
Test braking systems for proper function.
-
Check tire pressure and inspect for wear or damage.
-
Inspect hydraulic systems and check fluid levels.
-
Test lift mechanisms and check for any unusual noises or malfunctions.
-
Lubricate all moving parts, including joints and bearings.
-
Check lights, horns, and other safety features for operation.
-
Inspect the battery and electrical system, checking for any signs of wear or leaks.
- Lift Systems (Elevators, Hoists):
-
Test emergency stop features and ensure they are operational.
-
Inspect cables and ropes for wear or fraying.
-
Test load capacity and verify that it meets operational standards.
-
Check safety limits and sensors for calibration.
-
Inspect lift motor and gearbox for smooth operation.
-
Lubricate moving parts such as pulleys, motors, and bearings.
-
Verify control panel functionality and inspect wiring for signs of damage.
10. Documentation and Record Keeping
- Maintenance Logs:
-
Update the maintenance log with completed tasks and inspection dates.
-
Ensure all maintenance activities are logged accurately, including work performed, parts replaced, and any issues discovered.
-
Review past logs to identify recurring issues and schedule additional inspections if necessary.
-
Document the use of parts, oils, lubricants, and any consumables.
-
Ensure that maintenance records are stored securely for future reference or audits.
- Manufacturer’s Guidelines:
-
Review and adhere to the manufacturer’s recommended maintenance schedule.
-
Update maintenance schedules based on equipment performance and age.
-
Verify that any recommended modifications or upgrades are noted and implemented as needed.
-
Cross-reference maintenance activities with the manufacturer’s troubleshooting guides for accuracy.
- Compliance and Safety Records:
-
Verify that all preventive maintenance activities are compliant with industry regulations and standards.
-
Maintain records of inspections required for safety compliance (e.g., OSHA, local regulations).
-
Review all certificates, permits, and licenses to ensure they are up to date.
-
Document any safety violations and remedial actions taken.
-
Keep records of safety drills and training sessions for employees involved in equipment maintenance.
11. Site and Facility Maintenance
- Flooring and Workspace Areas:
-
Inspect floors for wear, cracks, and other potential safety hazards.
-
Check mats, rugs, or safety padding and replace as needed.
-
Ensure that aisles and pathways are clear of obstructions.
-
Clean and sanitize the workspace to prevent accidents or contamination.
-
Inspect areas around equipment for clutter or improperly stored tools.
- General Cleanliness and Housekeeping:
-
Ensure that all equipment and surrounding areas are free from dirt, dust, and debris.
-
Clean ventilation openings and ensure air flow is not obstructed.
-
Check for any buildup of hazardous materials or chemicals and clean up as necessary.
-
Organize tools and equipment, ensuring that everything is in its proper place.
-
Ensure that proper waste disposal practices are in place for hazardous materials.
Follow the Manufacturer’s Maintenance Schedule
Sticking to the recommended maintenance intervals helps catch potential issues early and extends equipment life.Inspect Equipment Before and After Use
Routine visual checks help spot leaks, cracks, or unusual wear before they turn into bigger problems.Keep Equipment Clean
Removing dirt, dust, and debris after use prevents clogging, overheating, and unnecessary wear.Check Fluid Levels Regularly
Monitoring oil, coolant, hydraulic fluid, and fuel levels keeps systems running efficiently and prevents breakdowns.Tighten Loose Bolts and Fasteners
Addressing loose components early prevents accidents and avoids costly repairs from neglected small issues.Replace Worn Parts Promptly
Swapping out worn belts, blades, filters, or tires on time keeps equipment reliable and operating at peak performance.Calibrate and Adjust Equipment as Needed
Regular calibration ensures that a piece of equipment operates accurately and maintains high-quality output.Store Equipment Properly
Sheltering equipment from harsh weather reduces corrosion and extends its working life.Train Operators Thoroughly
Properly trained operators handle equipment correctly, reducing misuse and unintentional damage.Keep Maintenance Records
Documenting repairs, inspections, and part replacements creates a clear history for troubleshooting and resale value.
What are the Tips to Follow for Equipment Maintenance?
These are useful tips to streamline equipment maintenance. Adhere to them alongside the preventive maintenance checklist we discussed above:
To Wrap Up
This comprehensive preventive maintenance inspection checklist template serves as a practical guide for maintenance professionals across various industries. It can be adapted to suit the specific needs of your equipment and operational environment. Be sure to regularly review and update your checklist to ensure the most efficient and effective maintenance practices are in place.