A Detailed Emergency Lighting Preventive Maintenance Checklist
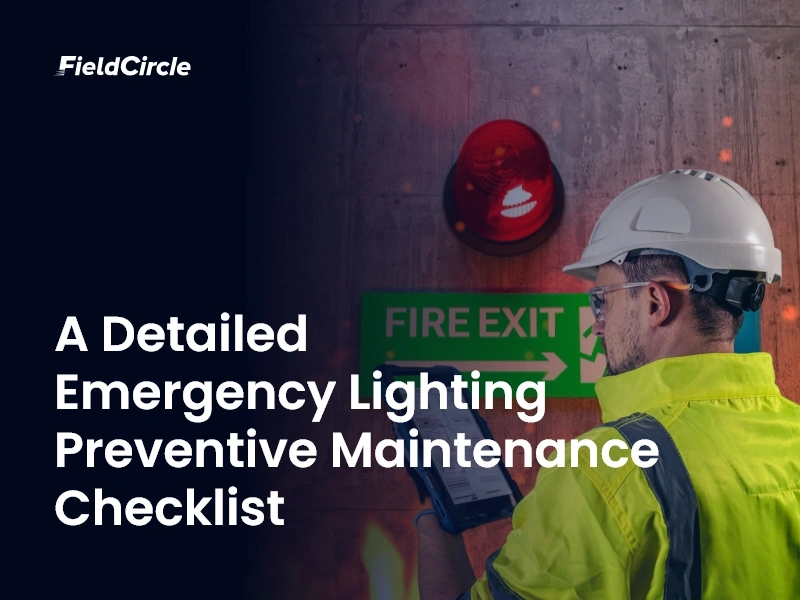
When the lights go out, the last thing you want to worry about is whether your emergency lighting system will kick in. It’s one of those things that’s easy to overlook, until it’s too late. Yet, keeping your emergency lighting in top shape is more than just a regulatory checkbox. It is an important step to make your lighting system work uninterruptedly.
Regular maintenance of these systems can be the difference between a smooth evacuation and a dangerous situation. So, if you’re in charge of keeping things running, having a well-thought-out preventive maintenance checklist is a must. The following preventive maintenance checklist for emergency lighting breaks down exactly what needs to be checked to keep your emergency lighting ready for anything.
What is an Emergency Lighting Preventive Maintenance Checklist?
An emergency lighting preventive maintenance checklist is a tool that outlines specific tasks for maintaining emergency lighting systems. It includes steps like testing battery backup, checking light intensity, inspecting wiring, and replacing faulty bulbs. The checklist aims to verify that all components function properly, preventing potential issues during emergencies and maintaining system reliability.
What are the Benefits of an Emergency Lighting Preventive Maintenance Checklist?
Using a preventive maintenance checklist for emergency lighting delivers direct benefits by identifying issues before they escalate. It plays a key role in maintaining the system’s reliability and functionality, ensuring that all parts work together efficiently. Here’s how it impacts both the emergency lighting system and its connected components:
- Addresses Immediate Failures in Key Components
Immediate identification of these problems prevents the risk of total failure during an emergency, ensuring the system operates as intended.
- Maintains Proper Battery Function
An emergency light maintenance checklist includes specific checks for battery charge levels, integrity, and lifespan which keep batteries at optimal capacity and they can thus deliver sufficient power during power outages without delay.
- Checks Light Output and Distribution
Regular checks of light output confirm that emergency lights provide the required illumination in the event of an emergency, offering clear visibility for evacuation routes.
- Monitors Circuit Continuity
Ensuring there are no loose connections or faults in the electrical system prevents failures that could compromise the emergency lighting function.
- Verifies Proper Fixture Alignment
The positioning of emergency light fixtures plays a significant role in ensuring sufficient coverage in the event of an emergency. A checklist verifies the alignment and placement of light fixtures along evacuation routes, minimizing the risk of dark spots.
- Tracks Battery Life Cycles
Routine checks also cover the lifespan of the batteries and their ability to hold charge, extending battery life and reducing unexpected replacement costs by predicting when a battery will need to be replaced, rather than waiting until it fails.
- Identifies Potential Risks
A preventive checklist helps identify any signs of strain or overuse in electrical circuits, avoiding the risk of damage to emergency lights and associated components, and also ensuring life safety.
- Assesses Remote Monitoring Systems
The checklist includes testing remote monitoring tools to confirm that emergency lighting status is communicated correctly to facility managers. Data transmission and alerts work as expected, and teams remain updated on the system’s health.
Emergency Lighting Preventive Maintenance Checklist
Following are the 15 essential items comprising a comprehensive checklist for preventive maintenance of emergency lighting systems:
1. Inspection of Light Fittings
- Fixture Condition
-
Check for cracks or physical damage on housings, lenses, and mounting brackets.
-
Inspect the fittings for signs of wear, such as discoloration or overheating.
-
Ensure all fixtures are securely attached to the mounting surfaces.
-
Verify that light fixtures are not obstructed by any object or material that could block the light output.
- Cleanliness
-
Wipe down lenses and housings to remove dust, dirt, or grime that may reduce light output.
-
Use appropriate cleaning agents that will not damage the fixture or lens materials.
-
Clean any ventilation grills or cooling areas to avoid overheating.
- Obstructions
-
Ensure that there are no physical obstructions around the emergency lighting fixtures (e.g., stored items or structural elements).
-
Check for any environmental factors that may block or impair the light’s beam or visibility (e.g., curtains, partitions).
2. Battery Maintenance
- Battery Voltage Check
-
Measure the battery voltage using a calibrated multimeter or similar testing equipment.
-
Compare the measured voltage to the manufacturer’s specifications and confirm that it is within the acceptable range.
-
Record battery voltage readings for documentation.
- Charge Status
-
Check the battery charge status using the control panel or dedicated battery status indicator.
-
Ensure the charging system is working correctly by inspecting charge status indicators (e.g., green for fully charged, amber for charging, red for fault).
-
Perform a manual charge test if the system has a built-in test feature to confirm charging functionality.
- Discharge Test
-
Disconnect the primary power source and initiate a full discharge test of the battery-powered emergency lighting.
-
Verify that the lighting maintains full brightness for the required duration (usually 90 minutes, depending on the system’s specifications).
-
Check that the light dims or turns off only when the battery reaches its minimal threshold.
- Battery Condition
-
Inspect the battery for visible signs of wear, such as bulging, leakage, or discoloration.
-
Check for any corrosion on the battery terminals.
-
Ensure that the battery’s manufacturer date and shelf life have not expired.
-
Verify that all connections to the battery terminals are tight and corrosion-free.
- Battery Replacement
-
If a battery is below the acceptable voltage, shows signs of deterioration, or fails the discharge test, replace it with a new one.
-
Confirm that the new battery matches the manufacturer’s recommended specifications in terms of voltage, capacity, and type.
-
Dispose of old batteries according to environmental regulations.
3. System Functionality
- Emergency Light Activation
-
Simulate a power outage by cutting off the main power supply.
-
Verify that all emergency lights automatically turn on in response to the loss of the main power.
-
Ensure that lights operate at full brightness as specified by the manufacturer.
-
Test the duration of light output to confirm that it meets the required backup time.
- Manual Switch Function
-
Test manual override switches by toggling them to ensure they engage or disengage emergency lights as expected.
-
Inspect all switches for damage, wear, or malfunction.
-
Confirm that manual switches reset properly after being turned off.
- Self-Test Feature (if applicable)
-
If the system includes a self-test feature, manually initiate the self-test cycle.
-
Verify that the system checks all connected components and records results.
-
Ensure that the self-test results are logged appropriately and alert the user to any detected faults.
- Confirm that the self-test mechanism properly activates emergency lights and performs functional checks.
4. Control Panel Inspection
- Control Panel Condition
-
Inspect the exterior of the control panel for any physical damage, cracks, or signs of wear.
-
Ensure the control panel is securely mounted and closed with no gaps, dust, or debris entering.
-
Check that all components inside the control panel (e.g., wiring, fuses, and circuit boards) are in good condition with no visible damage.
- System Status Indicators
-
Verify that all status lights (e.g., battery charging, system ready, fault indicators) are operational.
-
Confirm that any display screens or digital readouts accurately reflect the system status.
-
Test all audible alarms to confirm they are functioning and can alert in case of failure or system fault.
- Alarm/Indicator Testing
-
Simulate an alarm condition by disconnecting power or triggering a fault.
-
Check that the control panel’s audible and visual alarms activate promptly.
-
Test all warning indicators (e.g., “battery low,” “fault,” “charging”) for visibility and legibility.
-
Verify that indicator lights are clearly visible and positioned for easy monitoring.
- Circuit Breakers and Fuses
-
Inspect all circuit breakers and fuses within the control panel for any signs of damage, corrosion, or tripping.
-
Test each breaker to ensure it operates correctly and can be reset.
-
Replace any damaged fuses or breakers with the appropriate replacements.
- Ensure the breakers and fuses match the manufacturer’s recommendations in terms of specifications and ratings.
5. Wiring and Electrical Connections
- Wire Integrity
-
Inspect all wiring for signs of damage, wear, or fraying.
-
Ensure that the insulation around wiring is intact and free from cracks, tears, or abrasions.
-
Check for any exposed wires or short circuits.
- Connection Check
-
Examine all terminal connections, especially on the control panel, lights, and battery, to ensure they are tight and secure.
-
Verify that there is no corrosion on metal connections and that they are clean.
-
Ensure that all connections are properly insulated to prevent electrical shorts.
- Grounding
-
Check the grounding system of the emergency lighting system to ensure it is intact and securely connected.
-
Inspect grounding rods and grounding points for corrosion or damage.
-
Verify that the grounding system complies with local electrical codes and regulations.
6. Lamp and Bulb Functionality
- Lamp Performance
-
Test each emergency light to ensure it provides adequate illumination when activated.
-
Check that the light output meets the required lux level, based on the manufacturer’s specifications or building code requirements.
-
Inspect the light beam for consistency and proper alignment.
- Lamp Condition
-
Inspect each lamp for physical damage, such as cracks, burned-out spots, or discoloration.
-
Replace any burnt-out, dim, or malfunctioning lamps.
-
Ensure that lamps are tightly seated and securely mounted in their fittings.
- Lamp Specification Compliance
-
Confirm that lamps used in emergency lighting comply with the manufacturer’s recommended specifications for wattage, voltage, and type.
-
Ensure that replacement lamps match the original manufacturer’s part numbers.
7. Exit Signage
- Illumination Check
-
Verify that all exit signs are illuminated when the emergency power is activated.
-
Confirm that the brightness level of the exit signs meets regulatory standards for visibility.
-
Test exit signs during both normal operation and during power failure conditions.
- Sign Visibility
-
Ensure that exit signs are clearly visible from a reasonable distance (typically 20 feet or more).
-
Check for obstructions around the sign (e.g., furniture, decorations, or structural elements).
-
Ensure that the direction arrows, if present, are clearly visible and not obstructed.
- Sign Condition
-
Inspect the physical condition of exit signs for cracks, fading, or other damage.
-
Verify that the lettering is legible and not faded.
-
Ensure that the sign frames are intact, with no missing parts or broken components.
8. Full System Load Test
- Power Failure Simulation
-
Disconnect the primary power supply to simulate an actual power outage.
-
Confirm that all emergency lights activate as they should and remain on for the required duration.
- Duration of Backup
-
Ensure that the lighting system continues to operate for the required backup duration (usually 90 minutes).
-
Confirm that lights do not dim prematurely or fail during the test.
- Battery Runtime Verification
-
Track the runtime of each emergency light, ensuring the battery-backed lights provide consistent brightness throughout the duration.
-
Measure the battery voltage and check that the battery level does not drop below the recommended threshold during the test.
9. Documentation and Record Keeping
- Test and Inspection Logs
-
Maintain a log of all tests performed, including battery voltage, performance, and light duration.
-
Record the date of the inspection, the name of the technician, and any issues or repairs noted.
-
Ensure that all results are signed off by the technician and stored securely for future reference.
- Maintenance Frequency Tracking
-
Track the frequency of inspections and maintenance to ensure adherence to the manufacturer’s recommended maintenance schedule.
- Set up reminders for upcoming inspections, battery replacements, and full system tests.
10. Testing and Troubleshooting
- Functionality Testing
-
Perform routine tests to verify that each emergency light fixture and exit light activates correctly in the event of power failure.
-
Check that all emergency lights maintain full brightness for the full backup duration.
-
Ensure that the self-test function (if available) triggers automatically and records any faults or failures.
- Fault Diagnosis
-
When lights do not turn on during a power failure, diagnose whether the issue is with the battery, lamp, or control system.
-
Check for issues like disconnected wires, defective lamps, or faulty circuit breakers.
-
Inspect the control panel for any error codes or malfunction signals.
- Resolution of Issues
-
Replace any defective lamps, batteries, or components as identified during troubleshooting.
-
Reset the system and conduct a follow-up test to confirm proper operation.
-
If faults are recurrent, escalate the issue for a more thorough investigation or professional repair.
11. Environmental Considerations
- Temperature Control
-
Verify that emergency lighting systems are not exposed to extreme temperatures (either too high or too low), as this can affect battery life and lamp performance.
-
Check that batteries are operating within the manufacturer’s specified temperature range.
-
Ensure that ventilation and air circulation around lights and control panels are not obstructed.
- Humidity and Corrosion Control
-
Inspect for signs of moisture, condensation, or corrosion inside the control panel and light fixtures.
-
Check for water leaks near the emergency lighting fixtures, particularly in basements, kitchens, and other damp areas.
-
Ensure that the system is protected from high-humidity areas, which could lead to rust or failure of electrical components.
- Dust and Debris Control
-
Keep the system’s components free of dust and debris, which can impair light output and lead to overheating.
-
Clean air vents and fans regularly to ensure proper airflow and cooling.
-
Check that light fixtures, batteries, and other components are sealed against dust ingress, particularly in industrial or high-dust areas.
12. Regulatory and Code Compliance
- Compliance with Local Codes
-
Review emergency lighting systems to confirm compliance with local safety codes (e.g., National Fire Protection Association [NFPA], British Standards, or local fire codes).
-
Ensure that emergency lighting covers all necessary exit routes and areas that are required to have lighting by law.
-
Maintain documentation showing that all installations and maintenance are in compliance with the appropriate regulations.
- Annual Certification
-
Ensure that the emergency lighting system is tested and certified annually by a qualified professional, in compliance with local regulations.
-
Verify that all necessary certification paperwork is filed and available for inspection.
- Updates and Upgrades
-
Stay up to date with any changes in building codes or emergency lighting standards that could affect the system.
-
Make necessary updates or upgrades to the system to maintain compliance with evolving regulations.
-
Record all updates and modifications made to the system for future reference.
13. Emergency Lighting System Upgrades
- Assess System Age and Condition
-
Evaluate the overall age of the emergency lighting system to determine if it is due for replacement or significant upgrade.
-
Check for any components (e.g., batteries, lights, wiring) that have surpassed their expected lifespan and may need replacing.
- Modernization
-
If the system is outdated, consider upgrading to more energy-efficient LED emergency lights.
-
Implement newer technologies, such as smart emergency lighting systems that integrate with building management systems (BMS).
-
Evaluate whether upgrading the control panel for remote monitoring or incorporating automated diagnostics could improve system reliability.
- System Expansion
-
If the building layout changes or new rooms are added, ensure the emergency lighting system is expanded to provide adequate coverage for all new areas.
-
Perform load testing to ensure the upgraded system can handle additional lights or longer backup durations.
14. End of Life Management
- System Decommissioning
-
When the emergency lighting system reaches the end of its life, ensure that the decommissioning process is carried out safely.
-
Disconnect the power supply and safely remove all system components, including batteries and light fixtures.
- Disposal of Components
-
Properly dispose of old batteries according to environmental regulations.
-
Recycle light fixtures, lamps, and control panel components in accordance with local e-waste regulations.
- Documentation of System Decommissioning
-
Document the decommissioning process, including removal of system components and disposal of hazardous materials.
-
Retain a record of the system’s end-of-life date and disposal for future reference or audits.
15. Staff Training and System Awareness
- Operator Training
-
Ensure that all building personnel are trained on how to operate the emergency lighting system, including how to perform basic tests and reset the system.
-
Provide training on how to read error codes or system alerts displayed on the control panel.
- Emergency Protocols
-
Train relevant staff on emergency protocols regarding the operation and maintenance of emergency lighting during power outages.
-
Ensure staff knows how to handle system malfunctions and who to contact for repairs.
- Periodic Refresher Training
-
Provide periodic refresher courses for operators and staff to ensure ongoing awareness and readiness in case of an emergency.
-
Review maintenance and testing schedules with all relevant personnel regularly to ensure they are familiar with the procedures.
- Conduct Regular Inspections
Routine checks of emergency lights, batteries, and circuits help identify issues before they escalate, reducing the chances of unexpected failures during emergencies.
- Replace Faulty Bulbs Immediately
Dead or dim bulbs should be replaced quickly to maintain the required illumination levels during a power outage.
- Verify Light Distribution
Check that emergency lights are positioned to cover all critical evacuation routes, ensuring clear visibility for occupants.
- Clean Fixtures and Lenses
Regular cleaning prevents dust buildup on light fixtures and lenses, which can impair the system’s effectiveness in an emergency.
- Check Electrical Connections
Inspect all wiring and connections for wear and tear, as loose or damaged circuits can compromise the system’s reliability.
- Test the System Under Load
Run tests under load conditions to verify that the emergency lights continue functioning at full capacity during power failure.
- Document Maintenance Activities
Keep a detailed log of inspections, tests, and repairs to maintain a record for compliance and audit purposes.
- Evaluate Remote Monitoring Systems
Ensure remote monitoring tools are active and accurately transmitting data to inform managers of any system malfunctions.
- Schedule Battery Replacements
Replace batteries before they reach the end of their service life, avoiding last-minute failures during an emergency situation.
What are the Tips to Follow for Emergency Lighting Maintenance?
Adopting a structured approach to emergency lighting maintenance can significantly reduce the likelihood of failures. Offered below are some tips in this direction to effectively carry out emergency lighting maintenance:
To Wrap Up
A well-structured emergency lighting preventive maintenance checklist should not only focus on the technical aspects but also encourage vigilance across every aspect. Periodic training sessions and drills should be part of the routine to reinforce awareness. Additionally, documenting every maintenance activity and testing result is essential to help identify trends or recurring issues.