A Detailed Diesel Generator Preventive Maintenance Checklist
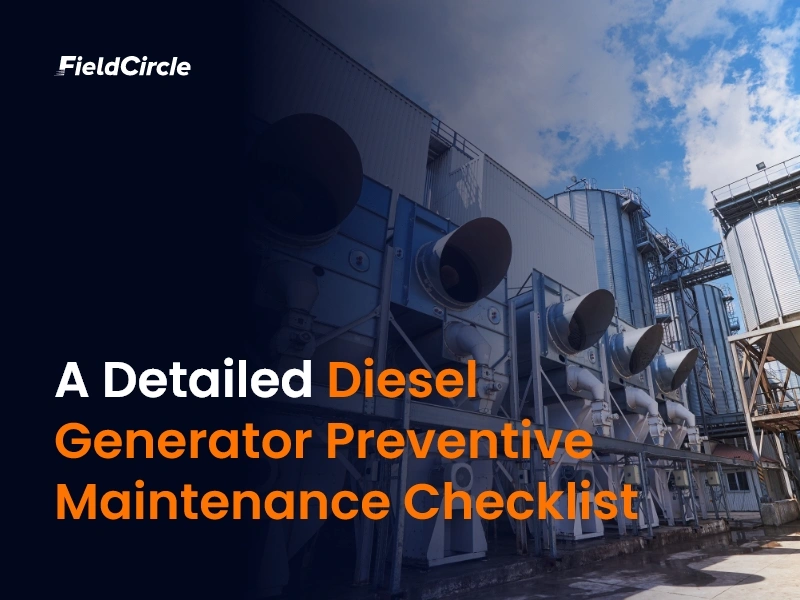
Diesel generators are widely used across industries to provide a reliable power backup during power outages and interrupted power supply, whether for commercial buildings, construction sites, or marine vessels. Their ability to operate under harsh conditions and provide consistent power makes them a popular choice. But we must remember, the durability and efficiency of diesel generators rely on proper maintenance.
Preventive maintenance of a diesel generator must be carried out through a checklist. In the ongoing part, we discuss the following diesel generator maintenance checklist that you must embrace if you want your industrial generator to deliver sustainable performance. Go through it to understand the elements that it constitutes.
What is a Diesel Generator Preventive Maintenance Checklist?
A diesel generator preventive maintenance checklist is a structured set of maintenance tasks designed to maintain the proper operation and longevity of a diesel generator. It outlines routine inspections, adjustments, and actions that need to be performed at specified intervals to minimize operational disruptions and maintain efficiency of the generator.
What are the Benefits of a Diesel Generator Pump Preventive Maintenance Checklist?
Apart from usual benefits like streamlined maintenance schedule, downtime reduction, a diesel generator preventive maintenance checklist offers several significant benefits. It helps build a robust power system for uninterrupted power supply by
- Preventing Fuel System Blockages
Regular pump checks identify fuel line or filter obstructions, allowing for early intervention and avoiding fuel delivery issues that could compromise the generator’s operation.
- Maintaining Proper Pressure Levels
Verifying that the pump’s fuel pressure matches the generator’s requirements avoids under- or over-pressurization, preventing engine inefficiency or damage.
- Reducing Cavitation Risks
Inspecting the pump for air bubbles or vapor helps avoid cavitation, which protects the pump and fuel system components from severe damage caused by improper fluid flow.
- Minimizing Component Wear
Routine maintenance of components like the impeller and bearings reduces internal friction, preventing premature wear and failure while extending the lifespan of the pump and generator.
- Ensuring Consistent Fuel Flow
Regular maintenance checks make sure the pump maintains steady fuel flow according to the generator’s needs, preventing fuel starvation and improving operational stability over time.
- Reducing Start-up Delays
Checking fuel delivery components regularly helps the generator start promptly and reach full capacity, cutting down on delays and ensuring reliable performance when power is needed.
Diesel Generator Preventive Maintenance Checklist
Here are the 10 checklist items to follow when carrying out the preventive maintenance of diesel generators:
1. Engine Oil and Lubrication System
- Check Engine Oil Level and Condition
- Inspect oil level using the dipstick and add oil if necessary.
-
Check oil condition for signs of contamination or sludge.
-
Verify that the oil is within the correct operating range (between the minimum and maximum marks).
- Inspect oil level using the dipstick and add oil if necessary.
- Change Engine Oil
-
Drain the old engine oil according to the manufacturer’s instructions.
-
Replace with fresh oil that meets the manufacturer’s specifications.
-
Record oil change in the maintenance log.
-
Check for proper oil flow once the new oil is added.
-
Drain the old engine oil according to the manufacturer’s instructions.
- Replace Engine Oil Filter
-
Remove the old oil filter carefully to avoid spills.
-
Install a new oil filter, ensuring it is properly seated and tightened.
-
Check for oil leaks around the filter after installation.
-
Remove the old oil filter carefully to avoid spills.
- Inspect Oil Pressure
-
Start the engine and monitor the oil pressure gauge.
-
Ensure the oil pressure is within the normal operating range.
-
If pressure is low, check for possible leaks or a faulty oil pump.
-
Start the engine and monitor the oil pressure gauge.
- Inspect Oil Cooler
-
Inspect the oil cooler for signs of leakage, cracks, or blockages.
-
Clean the oil cooler to remove any debris or dirt buildup.
-
Check for adequate oil flow and proper cooling during operation.
-
Inspect the oil cooler for signs of leakage, cracks, or blockages.
2. Fuel System Maintenance
- Check Fuel Level and Quality
-
Inspect the fuel tank to ensure the level is sufficient for operation.
-
Check the quality of fuel (look for contamination such as water, debris, or rust).
-
Test fuel for proper storage (ensure no degradation due to age or contamination).
-
Inspect the fuel tank to ensure the level is sufficient for operation.
- Inspect Fuel Filters
-
Examine the primary and secondary fuel filters for signs of clogging or dirt accumulation.
-
Replace fuel filters according to the manufacturer’s recommended intervals or when dirty.
-
Examine the primary and secondary fuel filters for signs of clogging or dirt accumulation.
- Verify Fuel Lines for Leaks
-
Inspect all fuel lines for cracks, abrasions, or leaks.
-
Replace any damaged fuel lines immediately.
-
Tighten loose fuel line fittings.
-
Inspect all fuel lines for cracks, abrasions, or leaks.
- Clean or Replace Fuel Injectors
-
Remove and inspect the fuel injectors for wear or clogging.
-
Clean injectors using an approved cleaning method (ultrasonic cleaning or professional service).
-
Replace any injectors showing significant wear or damage.
-
Remove and inspect the fuel injectors for wear or clogging.
- Inspect Fuel Tank for Corrosion or Damage
-
Examine the fuel tank for external corrosion or physical damage.
-
Check for rust or internal corrosion, which may contaminate fuel.
- Replace or repair the fuel tank if significant damage or corrosion is found.
-
Examine the fuel tank for external corrosion or physical damage.
3. Air Intake and Exhaust System
- Inspect Air Filters
-
Remove the air filter and inspect it for dirt, dust, or clogging.
-
Clean the air filter or replace it if it’s beyond cleaning.
-
Ensure the air filter is seated correctly in its housing.
-
Remove the air filter and inspect it for dirt, dust, or clogging.
- Check Air Intake System
-
Inspect air intake hoses for cracks, wear, or leaks.
-
Ensure that the intake manifold and ducts are clear of any debris or blockages.
-
Clean the intake system to remove dust and debris.
-
Inspect air intake hoses for cracks, wear, or leaks.
- Clean or Replace Air Intake System Components
-
Inspect the air intake components (such as the intake manifold and ductwork) for damage or excessive dirt buildup.
-
Clean the components with compressed air or a vacuum if needed.
-
Replace components showing signs of wear or irreparable damage.
-
Inspect the air intake components (such as the intake manifold and ductwork) for damage or excessive dirt buildup.
- Inspect Exhaust Pipes and Muffler
-
Check the exhaust pipes for cracks, leaks, or signs of damage.
-
Examine the muffler for rust or blockages.
-
Ensure that exhaust system components are tightly secured and there are no loose connections.
-
Check the exhaust pipes for cracks, leaks, or signs of damage.
- Clean Exhaust System
-
Remove soot and carbon buildup from the exhaust system using a cleaning method recommended by the manufacturer.
-
Inspect the exhaust system for signs of backpressure, which can indicate blockage.
-
Ensure that exhaust gases are properly vented to avoid overheating the generator.
-
Remove soot and carbon buildup from the exhaust system using a cleaning method recommended by the manufacturer.
4. Cooling System
- Check Coolant Level
-
Inspect coolant level in the radiator and refill as needed.
-
Check for any visible coolant leaks around the radiator, hoses, and connections.
-
Monitor the coolant level during generator operation to ensure it stays within safe operating limits.
-
Inspect coolant level in the radiator and refill as needed.
- Inspect the Condition of Coolant
-
Check the coolant’s appearance (it should be clean and free of contaminants).
-
If coolant appears cloudy or rusty, replace it to prevent overheating and internal corrosion.
-
Test coolant pH and anti-freeze properties with a coolant tester.
-
Check the coolant’s appearance (it should be clean and free of contaminants).
- Replace Coolant
-
Drain the old coolant according to the manufacturer’s instructions.
-
Refill the system with new coolant that meets the manufacturer’s specifications.
-
Dispose of old coolant properly according to local regulations and maintenance compliance requirements.
-
Drain the old coolant according to the manufacturer’s instructions.
- Inspect Radiator
-
Check the radiator for external damage, such as dents or cracks.
-
Inspect the radiator fins for blockages, dirt, or debris.
-
Clean the radiator with a soft brush or compressed air to improve airflow.
-
Check the radiator for external damage, such as dents or cracks.
- Test Cooling Fans
-
Inspect cooling fans for proper operation (check that they rotate freely and smoothly).
-
Ensure the fan belt is properly tensioned and free from wear.
-
Verify fan motor function by running the generator under load.
-
Inspect cooling fans for proper operation (check that they rotate freely and smoothly).
- Check Hoses and Clamps
-
Inspect all coolant hoses for cracks, leaks, or bulges.
-
Tighten or replace hose clamps that are loose or corroded.
- Replace any hoses showing significant wear or signs of deterioration.
-
Inspect all coolant hoses for cracks, leaks, or bulges.
5. Starting and Charging System Inspection
- Inspect and Test Battery
-
Check the battery for corrosion on terminals and cables.
-
Clean the battery terminals with a battery terminal cleaner and wire brush if needed.
-
Ensure the battery is properly secured and fastened.
-
Check the battery for corrosion on terminals and cables.
- Check Battery Fluid Level
-
Inspect the fluid level in each cell of the battery.
-
Refill cells with distilled water if fluid levels are low (avoid overfilling).
-
If the battery is sealed, check the manufacturer’s recommendations for fluid monitoring.
-
Inspect the fluid level in each cell of the battery.
- Inspect Battery Cables and Connections
-
Inspect all battery cables for signs of fraying, wear, or damage.
-
Check all connections to ensure they are tight and corrosion-free.
-
Tighten any loose connections, particularly the positive and negative terminals.
-
Inspect all battery cables for signs of fraying, wear, or damage.
- Check the Alternator
-
Test the alternator’s output using a voltmeter to confirm that it is charging the battery properly.
-
Inspect the alternator for any unusual noises or signs of wear.
-
Check the alternator belt for wear or slack and adjust or replace it as necessary.
-
Test the alternator’s output using a voltmeter to confirm that it is charging the battery properly.
- Inspect Starter Motor
-
Test the starter motor by attempting to start the engine and observing its performance.
-
Check for any unusual sounds or slow cranking which may indicate a problem with the starter motor.
-
Ensure the starter motor is securely mounted and connections are tight.
-
Test the starter motor by attempting to start the engine and observing its performance.
6. Electrical System and Wiring Inspection
- Inspect Wiring Harness
-
Check the wiring harness for signs of wear, abrasions, or exposed wires.
-
Secure any loose wiring and replace damaged or faulty wires.
-
Check the wiring harness for signs of wear, abrasions, or exposed wires.
- Inspect Fuses and Circuit Breakers
-
Inspect all fuses for signs of blowing or wear.
-
Replace any blown fuses with the correct rating.
-
Test circuit breakers to ensure they are functioning properly.
-
Inspect all fuses for signs of blowing or wear.
- Check Control Panel and Instruments
-
Inspect the control panel for proper functioning of all gauges, warning lights, switches, alarms, indicators, and associated systems.
-
Calibrate any malfunctioning gauges to ensure accurate readings.
-
Inspect the control panel for proper functioning of all gauges, warning lights, switches, alarms, indicators, and associated systems.
- Verify Grounding System
-
Inspect grounding connections to ensure there is no corrosion or damage.
-
Ensure the generator is properly grounded to prevent electrical hazards.
-
Tighten any loose ground connections to improve electrical safety.
-
Inspect grounding connections to ensure there is no corrosion or damage.
7. Mechanical System
- Inspect Engine Mounts
-
Examine engine mounts for any signs of wear, cracks, or excessive vibration.
-
Tighten any loose engine mounting bolts.
-
Replace engine mounts that are cracked, broken, or excessively worn.
-
Examine engine mounts for any signs of wear, cracks, or excessive vibration.
- Check Vibration Dampers
-
Inspect vibration dampers for signs of damage or excessive wear.
-
Replace any dampers showing excessive wear or cracks.
-
Ensure vibration dampers are properly aligned to reduce excessive vibration.
-
Inspect vibration dampers for signs of damage or excessive wear.
- Inspect the Flywheel and Crankshaft
-
Inspect the flywheel for cracks or excessive wear.
-
Check the crankshaft for proper alignment and any signs of damage.
-
Lubricate the flywheel and crankshaft components as needed to reduce friction and wear.
-
Inspect the flywheel for cracks or excessive wear.
- Examine Fuel and Oil Pump
-
Check the fuel and oil pumps for leaks or irregularities in operation.
-
Inspect the pumps for any unusual noises or signs of wear.
-
Clean or replace the pumps if there are any issues affecting their performance.
-
Check the fuel and oil pumps for leaks or irregularities in operation.
8. Generator Operation and Load Testing
- Perform Load Test
-
Verify that the generator can handle its rated load under normal operating conditions.
-
Use load banks or other equipment to perform a load test at different load levels (e.g., 50%, 75%, 100%).
-
Monitor voltage, frequency, and other performance parameters during the test.
-
Verify that the generator can handle its rated load under normal operating conditions.
- Check for Proper Operation Under Load
-
Verify that the generator operates smoothly without excessive vibration or unusual noise when under load.
-
Ensure that the generator maintains stable voltage and frequency output under varying loads.
-
Verify that the generator operates smoothly without excessive vibration or unusual noise when under load.
- Inspect Generator Exciter System
-
Check the exciter system for signs of wear or malfunction.
-
Inspect the exciter brush assembly for wear and replace if necessary.
-
Verify the functionality of the excitation control system.
-
Check the exciter system for signs of wear or malfunction.
- Test Safety Shutdown Mechanisms
-
Test all safety shutoff mechanisms such as low oil pressure, high coolant temperature, and high exhaust temperature.
-
Verify that the generator shuts down correctly in response to these critical parameters.
-
Test the emergency stop button to ensure it functions as expected.
-
Test all safety shutoff mechanisms such as low oil pressure, high coolant temperature, and high exhaust temperature.
9. Control System and Automation
- Control Panel and Interface
-
Inspect indicator lights, buttons, and screen display for proper function
-
Check for warning or error codes
-
Clean dust or debris from the panel surface
-
Inspect indicator lights, buttons, and screen display for proper function
- Programmable Logic Controller (PLC)
-
Verify input/output signals are working as expected
-
Confirm correct software version and configurations
-
Check PLC enclosure for moisture or loose wiring
-
Verify input/output signals are working as expected
- Automatic Transfer Switch (ATS)
-
Test manual and automatic switching operations
-
Check time delay settings and cycle timers
-
Inspect switch contacts for signs of arcing or pitting
-
Test manual and automatic switching operations
- Remote Monitoring and Alarms
-
Confirm communication with SCADA or cloud-based platforms
-
Check signal strength and sensor calibration
- Test alarm conditions and alert delivery (SMS, email, local buzzer)
-
Confirm communication with SCADA or cloud-based platforms
10. Enclosure and Frame Inspection
- Structural Integrity
-
Check for cracks, corrosion, or deformation on frame and housing
-
Inspect for signs of water damage or leaks
-
Check for cracks, corrosion, or deformation on frame and housing
- Doors, Panels, and Seals
-
Open/close all access doors to verify hinges and latches work
-
Check gasket condition for wear or compression loss
-
Ensure weatherproof seals are intact
-
Open/close all access doors to verify hinges and latches work
- Airflow and Ventilation
-
Inspect intake and exhaust louvers for blockages or damage
-
Clean mesh screens and grilles to maintain airflow
-
Verify proper operation of ventilation fans if installed
-
Inspect intake and exhaust louvers for blockages or damage
- Cleanliness and Pest Control
-
Remove dust, oil residue, or debris buildup
-
Check for rodent nests or insect activity
- Apply pest deterrents if necessary
-
Remove dust, oil residue, or debris buildup
What are the Tips to Follow for Diesel Generator Maintenance?
Following is a set of practical tips you should follow for having a well-maintained diesel generator:
- Regular Oil Changes
Diesel engines generate a lot of heat and pressure, which can cause the oil to break down over time. Changing the oil at regular intervals is crucial to prevent engine wear. Typically, you should change the oil every 250 to 500 hours of operation or as recommended by the manufacturer.
- Check and Replace Fuel Filters
Fuel quality directly impacts the performance of your diesel generator. Regularly inspect and replace fuel filters to avoid clogs caused by dirt, water, or impurities in the fuel.
- Inspect the Coolant System
Diesel engines tend to generate a lot of heat. Keeping the coolant system in good condition is essential to prevent overheating and potential engine damage. Check coolant levels, hoses, and the radiator regularly. Clean out any dirt or debris that might be obstructing airflow.
- Battery Maintenance
Diesel generators often rely on batteries to start. Regularly check battery voltage and ensure the terminals are clean and corrosion-free. Consider replacing the battery every 2-3 years or sooner if it’s showing signs of weakness.
- Examine the Air Filter
A clogged or dirty air filter can reduce the engine’s efficiency, leading to fuel waste and potential damage. Make sure to clean or replace the air filter as needed. Depending on your environment, you may need to replace it more frequently in dusty or high-pollution areas.
- Check Exhaust System for Leaks
Inspect the exhaust system for signs of leaks, cracks, or rust. Exhaust leaks can not only reduce efficiency but can also pose safety risks. Repair any issues promptly to maintain optimal performance.
- Test Generator Load and Run Time
Periodically test the generator under load to ensure it can handle the expected demand. Generators that are only run on light loads for extended periods may develop issues such as wet stacking, where unburned fuel accumulates in the exhaust system.
- Clean the Generator Regularly
Dirt, debris, and grime can accumulate on the generator’s surface, which can cause overheating or reduced performance. Regularly clean the generator, especially the radiator fins, air intakes, and exhausts.
- Monitor Fuel Quality
Diesel fuel can degrade over time and absorb moisture, which leads to microbial growth or the formation of sludge. Use fuel stabilizers and additives to maintain fuel quality, especially if the generator is running infrequently.
To Wrap Up
This diesel generator preventive maintenance and inspection checklist protects the equipment and maintains the operational continuity. Businesses thus safeguard their backup power source and know that it remains dependable when needed most.
As we saw, the checklist is a key tool that technicians must use for the visual inspection of different generator components and thus, with it, a diesel generator remains at par with industry standards and is ever ready to deliver peak performance.