Top 10 Manufacturing Maintenance Challenges and How to Overcome Them
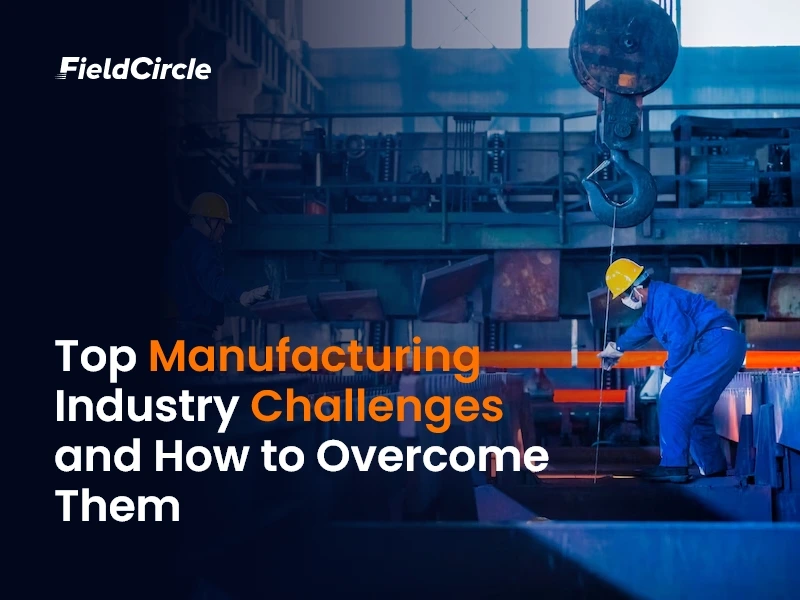
Supply chain disruptions, rising production costs, and labor shortages have kept manufacturers on their toes, making operational efficiency harder to maintain. The growing pressure to adopt automation and digital transformation only adds to the complexity, forcing businesses to rethink traditional processes. Without a strategic approach, staying competitive in this evolving landscape becomes an uphill battle.
Addressing these challenges requires a mix of technology, skilled workforce management, and proactive risk mitigation. Investing in smart manufacturing, leveraging data analytics, and optimizing supply chains are must-to-adopt practices to help businesses navigate uncertainties. At the same time, workforce upskilling and strategic partnerships are equally important in sustaining long-term growth.
Keeping in view these points, we explore the top 10 challenges in manufacturing, and offer actionable solutions to deal with them so that you are set to achieve long-term success.
1. Unplanned Equipment Downtime
80% of all unplanned downtime in manufacturing occurs due to equipment failure. Such disruptions halt the production line, cause delivery delays, disrupt production and delivery schedules, and increase operational costs. It also impacts the supply chains, creating bottlenecks and missing delivery deadlines.
Additionally, interruptions and hasty restarts degrade product quality, and unexpected equipment breakdowns can put the workplace at risk. For example, worn-out bearings can cause conveyor belt motor failure, which can cause hours of production halt and delays in fulfilling customer orders.
Solution:
Adopting real-time monitoring and predictive maintenance features in maintenance software mitigates unplanned downtime. It uses IoT-based sensors to track temperature, vibration, humidity, and pressure and analyzes the data via AI-driven analytics. It helps predict potential equipment failures and schedule timely interventions to reduce breakdowns and maintenance costs.
Proper employee training becomes important here. It must be provided to use predictive maintenance and analytics tools. Manufacturers must maintain inventory and spare parts management to ensure all critical components are readily available for repairs and replacements.
2. Inefficient Maintenance Planning
Inefficient maintenance planning arises when manufacturers rely on reactive maintenance instead of scheduled checks. Maintenance teams react to problems and emergencies after asset malfunction or failure, which requires higher costs than planned maintenance. Poor maintenance planning reduces overall productivity from 5 to 20%. It also leads to frequent disruptions and increased time and resource consumption.
Other causes are inaccurate machine performance or maintenance records, inadequate staffing to execute maintenance tasks effectively, and unclear priorities that misalign schedules and create communication gaps between operation and maintenance teams.
These reasons neglect machinery and equipment maintenance that accelerates wear and tear, reducing asset lifespan. As a result, it reduces operational efficiency and increases maintenance and operating costs. For example, poor lubrication practices in a textile company lead to frequent loom breakdowns, reducing product quality, lowering equipment efficiency, and increasing scrap rates.
Solution:
The manufacturing sector can create efficient maintenance planning through computerized maintenance management (CMMS) integration and preventive task scheduling. As an essential step, it will help track maintenance schedules, equipment history, and resource allocation.
Adopting Predictive Maintenance (PdM) helps gather real-time data through sensors and analytics tools to predict failures and implement maintenance schedules before they impact operations. These efforts make maintenance planning effective, prioritizing critical tasks, increasing equipment reliability, and enhancing productivity.
3. Shortage of Skilled Technicians
The manufacturing industry faces a critical shortage of skilled technicians, uniquely impacting its ability to maintain productivity and adapt to modern advancements. An aging workforce, rapid technological change, and a widening skills gap drive this shortage. Experienced technicians are hard to replace, and finding professionals with modern manufacturing skills for maintenance managers is a challenge.
Emerging technologies like automation and robotics are moving faster than skill development, and there is a mismatch between required technical skills and available training. It results in multiple issues as inexperienced staff struggle with complex repairs and delays.
Next, productivity suffers from slower issue resolution and inefficient maintenance planning, and innovation is being held back by limited adoption of new technologies. By 2033, the industry will need 3.8 million skilled technicians, and 1.9 million jobs could be unfilled if these gaps persist.
Solution:
To fix this, manufacturers should upskill employees by partnering with educational institutions for hands-on training and in-house workshops on emerging technologies to narrow the knowledge gap. Manufacturers must provide inexperienced staff with intuitive maintenance software. It includes real-time support, mobile accessibility, a user-friendly interface, and maintenance scheduling tools to manage repairs, increase uptime, and keep the operation running.
4. Supply Chain Disruptions for Spare Parts
Logistic issues such as shipping, customs, freight handling delays, limited suppliers, inconsistent quality, and outdated systems create supply chain disruptions for spare parts. Unanticipated demand fluctuations and global events like pandemics, natural disasters, or geopolitical tensions further compound these challenges.
Creating a shortage and unavailability of spare parts, these issues escalate and turn into bigger problems. Manufacturers experience shutdown or line stoppage due to the unavailability of spare parts. It also disrupts operational workflows, increases inefficiencies, and production delays. For example, port congestion hampers the delivery of critical spare parts. Maintenance activities are delayed, and machinery faces downtime for extended periods, slowing production and missing deadlines.
Solution:
One of the primary solutions to mitigate spare parts disruptions includes proper inventory management using a predictive maintenance strategy. The strategy provides information about future failures, which are used to maintain stock of parts and tools and schedule maintenance without any issues. It eliminates frequent and prolonged breakdowns, emergency repair costs, and repair and replacement delays.
Likewise, manufacturers should partner with multiple suppliers to reduce dependency on a single source and have a contingency plan, including alternate sourcing and local suppliers to mitigate the spare parts crisis.
5. Managing Aging Equipment
Aging equipment requires frequent repairs, causing production disruptions that eventually lower productivity. Aging equipment is the leading cause of 44% of unscheduled downtime in manufacturing facilities. Maintaining older or legacy equipment becomes challenging due to a shortage of parts due to discontinuity. Spare parts for older and outdated assets are not readily available.
Another issue with aging equipment is their inability to integrate modern technologies like AI, machine learning, and robotics, making it difficult for manufacturers to meet the demands of modern production lines, leading to inefficiencies. For example, a manufacturing plant with an obsolete Programmable Logic Controller experiences frequent breakdowns, halting production and missed deadlines.
Solution:
To minimize the impacts of aging equipment, manufacturers should create obsolete parts in-house so they do not face scarcity during maintenance tasks. They implement preventive maintenance to inspect equipment regularly and repair and replace parts to minimize downtime. Another major solution is to upgrade systems incrementally to reduce reliance on outdated equipment and get modernized solutions to meet production demand.
6. Rising Operational Costs
Reliance on aging equipment that breaks down often and needs frequent repairs, inflation, increased labor costs, higher energy consumption, and unexpected maintenance expenses increase operational costs. Poorly maintained machines reduce output and disrupt production schedules due to frequent breakdowns. This hampers product quality and tarnishes customer satisfaction. Improving service efficiency in manufacturing is thus important so as to sustain customer relationships.
All these components increase expenses while diminishing total production, impacting profitability. For example, a semiconductor manufacturer experienced 15% higher operating costs than its top three competitors due to inefficient research and development processes.
Solution:
The countermeasure to keep operation costs in check is to use predictive maintenance for better resource allocation. Using energy consumption tracking and cost analytics helps track expenses and identify inefficiencies. Proper data analysis provides actionable insights for designing strategies to reduce energy usage and allocate budget more effectively.
Manufacturers can get reports about most energy-consuming equipment and replace them with energy-efficient models. Also, right inventory management helps stock critical parts and streamline maintenance tasks, thereby helping avoid delays and reducing associated costs.
7. Ensuring Compliance with Safety Standards
Compliance with safety standards in the manufacturing industry can arise due to inadequate employee training, aging equipment’s failure to pass safety tests, and lack of safety procedures or outdated manuals. The stringent nature of these compliances makes the process complex.
For instance, OSHA standards emphasize hazard identification and mitigation, necessitating workflow adjustments to accommodate regular inspections and employee training. PSM ensures the safe handling of hazardous chemicals, but then it requires manufacturers to enhance process controls and implement robust risk assessments.
Failure to meet these safety standards results in fines, production delays, shutdowns, and reputational damage. In 2024, the penalty for non-compliance with OSHA’s PSM standard was $16,131 per violation, which casts light on how costly the repercussions could be.
Solution:
To meet necessary safety standards, manufacturers must conduct regular audits, maintain detailed documentation, and manage proper compliance tracking. They must use inspection checklists and audit-ready reporting tools to simplify compliance management.
Other essential steps include upgrading or replacing older equipment with ones that meet safety standards, conducting regular safety inspections and risk assessments, providing safety training to employees, and deploying updated and easily accessible digital manuals.
8. Lack of Visibility Across Operations
Disconnected systems and siloed information in separate systems create difficulty in tracking maintenance progress and analyzing operational data. The lack of visibility across operations, caused by limited automation and outdated systems lacking real-time reporting capabilities, hinders decision-making and leads to inefficiencies.
Further, poor communication and ineffective collaboration between maintenance, production, and management teams result in inconsistent workflows and inefficient data sharing. The inefficiencies delays maintenance tasks and mismanages resource allocation. For instance, a lack of integration between CMMS and production data delays reporting maintenance issues and it delays the issue resolution time and lowers equipment reliability.
Solution:
Integrating dashboards using manufacturing maintenance software provides centralized data storage that helps track, schedule, plan, and manage maintenance activities. The approach enhances inter-department communication, makes data sharing easy, and allows different teams to retrieve operations data easily. Additionally, the integration capabilities between maintenance and production also automate reporting to send maintenance alerts and reports for better decision-making.
9. Difficulty Adapting to Industry 4.0 Technologies
The manufacturing sector faces difficulty adapting to 4.0 technologies like AI, IoT, and predictive maintenance tools due to the incompatibility of existing equipment with modern technologies and the lack of employee training in using these advanced technologies.
Due to the high implementation costs of smart devices, sensors, and maintenance software, manufacturing companies deter this advanced technology and continue using legacy systems. Resistance of employees to adopting the new system also poses a great threat. Integration difficulties slow down the implementation process, affecting productivity.
Solution:
To make the adoption of 4.0 technologies in the manufacturing sector easier, companies should gradually integrate smart tech via phased implementation to spread costs and reduce disruption. They replace legacy systems with scalable and industry-4.0-compatible equipment to compete in the modern, competitive landscape.
For instance, a small metal fabricator manufacturer in Central Quebec implemented 4.0 technology using Gamache’s six-step approach and experienced a 40% reduction in time spent on information and parts search in the assembly department, reduced product design time by 90%, and reduced drawing time by 32%.
10. Material Handling and Inventory Challenges
The manufacturing industry experiences material handling and inventory challenges due to incompatible legacy systems, lack of integration between departments and systems, errors in manual tracking and handling, inadequate IoT and automation deployment, and insufficient skilled force to handle advanced systems.
These issues lead to increased inefficiencies and operation costs, inaccurate data leads, production delays, and lost revenue. It also results in production bottlenecks and delays. For example, in 2024, Boeing faced significant material handling and inventory issues, resulting in approximately 200 nearly completed airplanes being stored in unconventional locations, including employee parking lots. The aircrafts were awaiting essential components such as interiors and engines, which led to substantial delays in delivery and increased holding costs.
Solution:
Proper inventory management and implementation of an IoT-enabled tracking system offer real-time visibility and streamline material handling processes. It uses automated inventory updates and optimized storage solutions to maintain a smooth flow of materials.
Integration of centralized ERP and MES systems helps eliminate silos and provide a centralized system for inventory management data for easy access. Providing proper employee training about inventory management systems using tutorials, guides, and workshops for increased efficiency is vital.
Conclusion
FieldCircle offers various software products and helps solve these challenges in manufacturing by providing real-time monitoring, predictive maintenance, and inventory management capabilities through its manufacturing maintenance software.
Whether it’s dealing with supply chain disruptions, managing rising operational costs, or adapting to Industry 4.0 technologies, FieldCircle enables manufacturers to maintain productivity, control expenses, and drive sustainable growth. Take a demo tour of our products to see how they align with your operational goals.