A Detailed Laboratory Equipment Preventive Maintenance Checklist
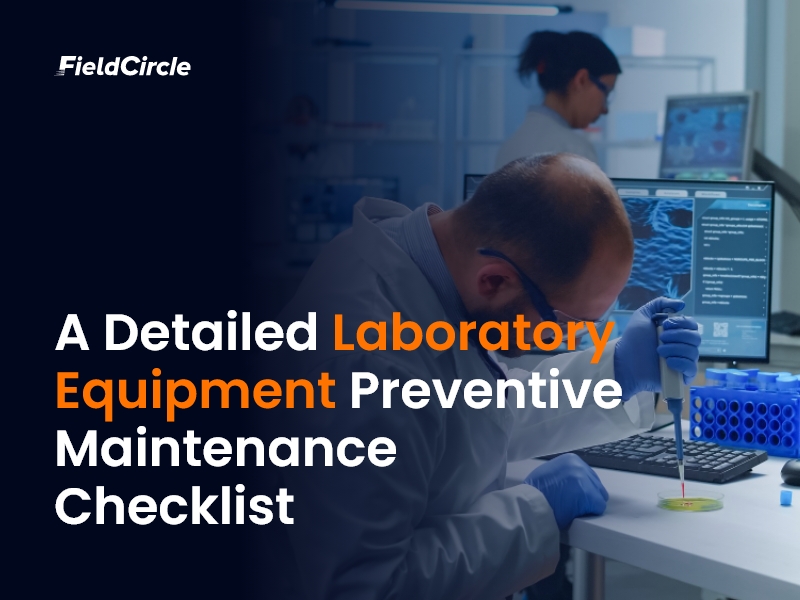
A detailed maintenance checklist is a foundational tool for operational discipline within any laboratory setting. When each piece of equipment is cared for systematically, laboratories gain more than extended equipment life – they gain consistency in results, fewer unexpected disruptions, and stronger compliance with internal and regulatory standards.
Not paying attention to routine tasks can quietly compromise results, while a documented checklist drives accountability and smooth delegation. Regularly updating the checklist pushes labs to reassess workflows and adapt to evolving equipment and standards, which makes it both a control tool and a strategic asset.
More importantly, the process of designing and regularly updating a maintenance checklist encourages laboratories to critically assess their workflows and adapt to new equipment, usage patterns, and quality benchmarks. It acts as both a control mechanism and a forward-looking strategy for sustainable lab management.
In light of this fact, we discuss a comprehensive preventive maintenance checklist for laboratory equipment along with best practices for performing maintenance of your equipment. Read on.
What is an Laboratory Equipment Preventive Maintenance Checklist?
A preventive maintenance checklist for laboratory equipment is a structured guide that lists routine maintenance and inspection tasks specific to lab instruments like centrifuges, incubators, spectrophotometers, and fume hoods. It supports timely calibration, cleaning, lubrication, and performance checks of these equipment to maintain their accuracy as well as uphold safety standards in laboratory operations.
What are the Benefits of a Laboratory Equipment Preventive Maintenance Checklist?
A well-structured checklist for preventive maintenance of laboratory equipment introduces discipline, accountability, and predictability and shapes the quality of scientific output, offering the following benefits:
- Provides Structured Task Execution
The checklist breaks down preventive actions into itemized steps, guiding technicians through consistent procedures without skipping vital checks or actions.
- Reduces Oversight
When labs manage multiple instruments, each with unique requirements, the checklist helps avoid missing individual component checks during batch maintenance rounds.
- Supports Technician Accountability
By requiring initials, timestamps, and recorded results, the checklist establishes responsibility for completed tasks and discourages undocumented shortcuts during preventive routines.
- Maintains Consistency
Standardized checklists allow every technician to follow the same maintenance protocol, regardless of shift timing or personnel changes, eliminating variability.
- Simplifies Audit Preparation and Internal Reviews
Completed checklists serve as ready records for inspections or internal reviews, showing what was done, when, by whom, and with what outcome.
- Acts as a Reminder
The checklist highlights date-based or usage-based triggers, such as replacing filters after 100 hours, helping prevent forgotten tasks that reduce equipment reliability.
Laboratory Equipment Preventive Maintenance Checklist
Following are the 6 parts that a laboratory equipment maintenance checklist essentially comprises:
1. Mechanical Components
- Inspection of Moving Parts
- Visually inspect moving components like motors, gears, belts, and pulleys for signs of wear and tear.
- Check for any abnormal vibrations or noises during operation.
- Use vibration sensors or handheld devices.
- Address noisy components by tightening, lubricating, or replacing faulty parts.
- Lubricate moving parts as per manufacturer’s guidelines.
-
Tighten any loose components such as bolts, screws, and nuts.
- Alignment and Leveling
- Check for proper alignment of rotating parts (e.g., spindle, rotor, etc.).
- Verify that equipment is level using a spirit level, making adjustments if necessary.
- Ensure that the equipment sits on a stable, flat surface.
-
Confirm that refrigeration units such as a freezer are perfectly leveled to prevent coolant flow imbalance.
- Inspection of Bearings and Bushings
- Examine all bearings and bushings for smooth operation.
- Check for any signs of excessive play or wear.
-
Replace damaged bearings or bushings immediately.
- Check of Air and Fluid Circulation
- Verify that air vents and filters are clean and unobstructed.
- Inspect hoses and pipes for cracks, leaks, or blockages, and replace if necessary.
- Check all fluid systems for signs of leaks, especially around seals and connections.
- Perform a pressure test to detect hidden leaks if necessary.
- Ensure that fluid circulation systems (if applicable) are working effectively.
-
In the case of a freezer, inspect refrigerant lines and airflow channels thoroughly.
- Check for Excessive Heat Generation
- Ensure ventilation systems are functional.
- Inspect and clean heat sinks or cooling fans.
- Verify that cooling fluids (if used) are at the correct temperature.
- Inspect cooling systems, fans, and heat exchangers.
-
Ensure that heaters or temperature regulators function according to specifications.
- Inspect for Corrosion or Rust
- Check metal components for rust or corrosion, especially on parts exposed to liquids or harsh environments.
- Clean and treat any corroded surfaces with appropriate rust inhibitors.
-
Replace severely corroded parts that may compromise the integrity of the equipment.
- Check Tension and Condition of Belts and Chains
- Inspect belts and chains for wear, cracks, and signs of stretching.
- Adjust the tension of belts or chains as required.
-
Replace belts and chains that show signs of severe wear or damage.
- Inspection of Springs and Shock Absorbers
- Check springs and shock absorbers.
- Replace damaged or worn-out springs/shock absorbers
-
Ensure vibration dampening systems (pads, mounts) are intact and functional.
- Test Equipment Load Handling (If Applicable)
- Perform load tests to ensure that lifting or handling components are capable of supporting the intended weight.
- Inspect pulleys, hoists, and other load-bearing components for wear.
-
Lubricate and maintain load-handling systems.
2. Electrical System and Power Supply
- Power Supply Inspection
- Check the voltage levels to ensure they are within the required range for the equipment.
- Inspect power cables for any signs of wear, fraying, or damage, and replace them if necessary.
- Ensure proper grounding of all electrical components.
-
Verify the power cord and plug are securely connected and free of damage.
- Circuit Breakers and Fuses
- Inspect circuit breakers and fuses for proper function and reset them if needed.
- Test fuses to confirm they are intact and replace any blown fuses.
-
Ensure that circuit breakers are correctly rated for the equipment’s electrical load.
- Electrical Panel and Connections
- Clean the electrical panel to prevent dust accumulation, which could affect performance.
- Check all electrical connections for tightness and corrosion, and retighten any loose connections.
- Inspect terminal blocks and connectors for signs of wear, overheating, or corrosion.
-
Replace any corroded or damaged electrical connectors immediately.
- Power Supply Backup (If Applicable)
- Test the backup power supply (e.g., uninterruptible power supply or UPS).
- Inspect the batteries in backup power systems for proper charge and replace any batteries nearing the end of their lifespan.
-
Clean vents and cooling fans of backup power systems.
- Surge Protectors
- Inspect surge protectors for wear or signs of failure, such as discoloration or damage.
- Test the function of surge protectors and replace any that are no longer providing protection.
-
Ensure that surge protectors are rated correctly for the equipment they are protecting.
- Grounding System
- Inspect grounding cables and connections for integrity and ensure they are free from corrosion or damage.
- Test the continuity of the grounding system to ensure proper grounding of all electrical components.
-
Check grounding electrodes (if applicable) for proper connection and effectiveness.
- Electrical Insulation
- Inspect the insulation on wires and cables for wear, cracks, or other signs of damage.
- Ensure that exposed electrical components are properly insulated.
-
Replace any damaged or worn insulation immediately.
- Control Panel and User Interface
- Test the functionality of control panels, switches, and indicators.
- Inspect the user interface for any wear or damage to buttons, screens, or dials.
-
Calibrate and clean the control panel if necessary.
- Overload Protection
- Check for the proper operation of overload protection circuits.
- Test thermal protection devices to ensure they will shut down the equipment in case of overheating.
- Reset or replace any activated protection devices as needed.
3. Calibration and Accuracy Checks
- Calibration of Measuring Instruments
- Check calibration certificates to ensure they are up to date and valid.
- Perform calibration of measurement devices (e.g., thermometers, pressure gauges, flow meters) against certified standards.
- Use calibration tools or reference equipment that are traceable to national/international standards.
-
Document calibration results, including any adjustments made to the equipment.
- Verification of Operational Parameters
- Compare the actual output of equipment against known standards or specifications (e.g., temperature, speed, pressure, volume).
- Ensure that the equipment’s parameters are within the acceptable tolerance range specified by the manufacturer.
-
Conduct a series of operational tests to verify that the equipment maintains accuracy under typical usage conditions.
- Software and Firmware Calibration
- Verify that software-controlled equipment is correctly calibrated according to the manufacturer’s recommended settings.
- Check that firmware updates are installed as required, and test that the software interfaces with hardware components without errors.
-
Recalibrate software settings if performance issues are observed, ensuring that all software adjustments are documented.
- Mechanical Calibration
- Verify the alignment and position accuracy of mechanical components (e.g., positioning systems, stages, or guides).
- Check the precision of mechanical movements using reference tools such as micrometers or laser systems.
-
Adjust or replace components if misalignment or mechanical drift is observed.
- Environmental Calibration
- Calibrate temperature and humidity control systems.
- Perform checks on airflow or ventilation systems to confirm that airflow rates and air quality meet required standards.
-
Verify that sensors for environmental monitoring are reading within specified ranges, recalibrating as needed.
- Accuracy of Measurement Devices
- Test all measurement devices for accuracy using certified standards or known reference values.
- Check for drifts in readings and recalibrate instruments if readings fall outside the allowed tolerance.
-
Regularly review measurement logs to identify any patterns of inaccuracies and investigate potential causes.
- Check for Drift and Repeatability
- Perform repeated measurements under controlled conditions to ensure that the equipment returns consistent results.
- Test the equipment’s repeatability by performing multiple tests using the same conditions and measuring instruments.
-
Investigate and resolve any issues related to drift or variation in measurement accuracy over time.
- Record Keeping and Documentation
- Keep a detailed record of all calibration checks, including dates, results, and adjustments made.
- Store calibration certificates, test results, and related documentation in an easily accessible and organized manner.
-
Ensure that the calibration documentation complies with industry standards or regulatory requirements.
- Calibration of Analytical Instruments
- For analytical instruments, check the calibration of sensors, detectors, and analysis software.
- Test with known reference samples to verify the accuracy of readings.
-
Recalibrate instruments if any discrepancies are found between the expected and measured values.
4. Structural Integrity (including Machine Bed and Tooling)
- Inspection of Machine Frame
- Visually inspect the overall machine frame for any signs of cracks, deformation, or damage.
- Ensure that the frame is securely mounted to the floor or base to prevent unnecessary vibrations during operation.
-
Check the alignment of the frame components, especially after heavy use or maintenance.
- Inspection of Machine Bed
- Inspect the machine bed for any signs of wear, pitting, or deformation, especially in areas that come into direct contact with tooling.
- Ensure that the machine bed is clean and free from dirt, dust, or oil that could affect accuracy and performance.
-
Check that the machine bed is level and properly aligned to maintain consistent operation.
- Tooling and Tool Holders
- Inspect tooling (e.g., drills, cutters, inserts) for signs of wear, damage, or dullness, and replace or sharpen tools as needed.
- Ensure that tool holders are securely fastened and show no signs of wear or damage.
-
Check for proper tool alignment and adjust if necessary to ensure precise cutting or operation.
- Guide Rails and Linear Motion Systems
- Examine guide rails, linear bearings, and motion systems for signs of wear or binding.
- Lubricate rail systems with the appropriate grease or oil to maintain smooth operation.
-
Inspect motion components for proper alignment and replace or adjust components if misalignment is detected.
- Check for Surface Flatness
- Measure the flatness of the machine bed and any critical surfaces using a precision flatness gauge or similar tool.
-
If the flatness exceeds the manufacturer’s tolerance, perform adjustments or resurfacing of the machine bed.
- Inspect Welds and Joints
- Visually inspect welded joints for signs of cracks, corrosion, or fatigue.
- If any welds are found to be compromised, perform necessary repairs or replacements to ensure structural integrity.
-
Check bolted joints for tightness and re-torque if necessary to prevent loosening during operation.
- Check for Overhead Supports and Mountings
- Inspect overhead supports and mountings for any loose or damaged connections that could lead to instability during operation.
-
Verify that all fasteners are properly tightened, and no components are at risk of detachment.
- Inspect Vibration Dampening Components
- Check any vibration-dampening elements, such as pads or mounts, for wear or degradation.
-
Replace dampeners if they have lost effectiveness in reducing vibrations, as this could impact precision and lifespan of the equipment.
- Tool Change Mechanism (If Applicable)
- Inspect the tool change mechanism for smooth operation and secure attachment of tools.
- Ensure that the tool changer is calibrated and functions correctly to avoid improper tool changes or damage during operation.
-
Lubricate moving parts of the tool changer mechanism to prevent friction-related failures.
- Check of Structural Alignment After Heavy Use
- After heavy usage or significant machine movement, verify that the overall alignment of the equipment is maintained.
- Check if any structural components have shifted or become misaligned during operation, and correct as needed.
5. Consumable Parts
- Inspection of Filters
- Inspect air, oil, and coolant filters for signs of clogging, dirt accumulation, or damage.
- Replace filters that show signs of reduced performance, such as a noticeable drop in airflow or filtration efficiency.
- Clean reusable filters according to the manufacturer’s instructions.
-
Verify that replacement filters match the equipment’s specifications in terms of size, material, and filtration capacity.
- Inspection of Seals and Gaskets
- Check seals and gaskets for signs of wear, cracking, or leaks.
- Inspect sealing surfaces for proper alignment and cleanliness, ensuring they make full contact with mating surfaces.
- Replace worn or damaged seals and gaskets to prevent leaks or contamination of the internal system.
-
Ensure that the correct material and size are used for replacement seals.
- Check of O-rings
- Inspect O-rings for any signs of degradation, such as brittleness, cracking, or swelling.
- Check for proper compression and fit to ensure an airtight or watertight seal.
-
Replace any O-rings that are damaged or compromised.
- Lubricant and Grease
- Inspect lubricant levels in moving components and ensure that they are within the recommended range.
- Check grease or oil for signs of contamination, discoloration, or degradation, and replace if necessary.
-
Lubricate components like bearings, gears, and shafts according to the manufacturer’s guidelines, using the recommended types of lubricants.
- Check of Cutting Tools and Inserts
- Inspect cutting tools, inserts, and other consumable tooling parts for signs of wear, chipping, or dullness.
- Replace or sharpen tools that no longer meet the equipment’s cutting performance standards.
-
Ensure that cutting tools are securely installed and properly aligned.
- Examine Conveyor Belts and Scrapers (If Applicable)
- Inspect conveyor belts for signs of wear, tears, or stretching and replace them if necessary.
- Check the alignment and tension of conveyor belts to ensure smooth operation.
-
Inspect scrapers for damage or wear and replace if needed.
- Check of Fluid Levels (Coolants, Oils, Hydraulic Fluids)
- Verify that fluid levels (coolants, oils, hydraulic fluids) are within the required operational range.
- Inspect fluids for signs of contamination, discoloration, or degradation and replace if needed.
-
Ensure that the correct type of fluid is used in the system as per the equipment manufacturer’s specifications.
- Inspection of Batteries
- Check the charge levels of rechargeable batteries (e.g., UPS or battery-powered equipment).
- Inspect batteries for signs of leakage, corrosion, or swelling.
-
Replace batteries that no longer hold charge or show signs of wear and tear.
- Check of Electrical Contacts and Contacts Plates
- Inspect contact plates, terminals, and electrical contacts for corrosion or signs of wear.
- Clean contacts to remove any build-up of dust, dirt, or corrosion that could interfere with electrical connections.
-
Replace damaged or corroded contacts to prevent short circuits or power failures.
- Inspection of Wear Pads and Liners
- Examine wear pads and liners for excessive wear, cracking, or damage.
-
Replace worn or damaged wear pads and liners to prevent excessive wear on other equipment components.
6. Safety Features and Systems
- Safety Guards and Shields
- Inspect all safety guards, shields, or barriers for damage or misalignment.
-
Ensure that safety features are not obstructed and that they function as intended during operation.
- Emergency Stops and Shutdown Systems
- Test the emergency stop button and shutdown systems.
-
Check wiring and components associated with emergency systems for any signs of damage or wear.
- Safety Alarms and Indicators
- Test all safety alarms, warning lights, and visual indicators.
-
Ensure that alarms are loud enough and clearly visible to alert operators of any issues.
- Lockout/Tagout (LOTO) Compliance
- Check that all lockout/tagout procedures and devices are in place and functioning correctly.
- Ensure that authorized personnel are properly trained in lockout/tagout procedures.
What are the Tips to Follow for Laboratory Equipment Maintenance?
For effective lab equipment maintenance, it is important to keep the following key tips in mind throughout the maintenance process:
- Follow Manufacturer Guidelines
Always refer to the user manual for each piece of equipment because specifications such as cleaning methods, part replacement intervals, and usage limitations vary from one device to another.
- Schedule Routine Inspections
Set an effective laboratory maintenance schedule for checking calibration, wear and tear, and general performance. Logging inspection dates and observations helps track the condition and predict service needs before issues arise.
- Use Proper Cleaning Methods
Use the correct cleaning agents and materials specific to each device. Harsh chemicals or abrasive materials can damage sensitive components, so selection of appropriate cleaning supplies is vital.
- Store Equipment Safely
Keep all tools in designated storage areas with controlled temperature, dust protection, and stable positioning. Random placement or exposure to moisture and heat causes degradation over time.
- Train Staff Thoroughly
Make sure all users know the right procedures for operating and maintaining equipment. Mishandling due to lack of training leads to damage and inaccurate results.
- Replace Worn Parts Promptly
Once a part shows signs of damage or fatigue, switch it with a suitable replacement without delay, as prolonged use of defective parts affects overall machine reliability and performance.
To Wrap Up
Maintaining laboratory equipment is a continuous commitment that supports the integrity of every experiment, analysis, and outcome. A comprehensive checklist turns that commitment into an actionable routine, leaving little room for oversight or inconsistency. So, a maintenance checklist may appear simple on the surface, but when followed consistently, it becomes one of the most valuable assets in a lab’s quality management framework. For regular maintenance of laboratory equipment, download our comprehensive checklist.