A Detailed Forklift Preventive Maintenance Checklist
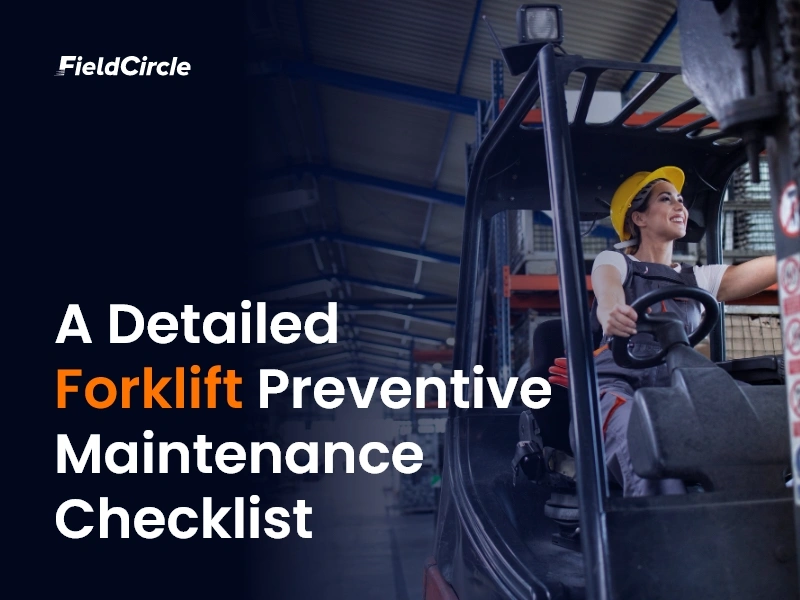
Forklifts are the backbone of many distribution centers (DC) and warehouse operations and letting things slide only invites headaches down the line. But keeping forklifts in tip-top shape doesn’t happen by chance as it calls for a solid maintenance plan. A preventive maintenance checklist acts like a trusty roadmap, guiding forklift operators through every nook and cranny of the machine.
Rolling up sleeves and sticking to a detailed checklist helps spot weak spots and nip problems in the bud. Below, we discuss this detailed forklift maintenance checklist along with helpful tips to carry out maintenance of forklift. You can use this checklist for different types of forklifts including diesel forklifts and electric forklifts.
What is a Forklift Preventive Maintenance Checklist?
A forklift preventive maintenance checklist is a structured list of routine inspections and maintenance tasks used to keep a forklift safe, stable, and ready for use. It focuses on checking wear and tear, spotting leaks, testing controls, and inspecting load-bearing parts.
What are the Benefits of a Forklift Preventive Maintenance Checklist?
Preventive maintenance checklists for forklifts help businesses stay ahead of schedule without wasting money on constant repairs or replacements by keeping equipment in reliable working order. To shed more light on why they’re worth the effort, following are the key benefits of using a forklift preventive maintenance checklist:
- Boosts Equipment Lifespan
Regular forklift maintenance checks help keep wear and tear under control and extend the lifespan of the equipment. Instead of letting parts wear out unnoticed, the checklist prompts timely action. That way, machines don’t go to the scrap yard before their time.
- Reduces Downtime
With fewer surprise breakdowns, teams stay on the job and production doesn’t miss a beat. Downtime reduction results in optimal performance and overall improvement in the productivity of operations.
- Cuts Maintenance Costs
When problems are caught early, you avoid costly repairs as there’s less need for expensive fixes or last-minute parts orders. A checklist keeps everything under control, helping companies stick to a maintenance budget without burning a hole in their pocket.
- Promotes Safer Work Conditions
By keeping tabs on safety features like brakes, lights, and hydraulics, the checklist helps create a safer space for operators and workers nearby, as well as maintenance technicians. It also avoids legal headaches that come with workplace accidents.
- Keeps Performance Consistent
Forklifts in top shape don’t lag behind. With regular checks, engines run smoothly, parts stay aligned, and fuel doesn’t go to waste. The checklist helps avoid performance dips that slow down operations and cause delays.
- Helps with Compliance
A preventive checklist acts as proof that equipment gets the right attention at the right time. When auditors come knocking, businesses don’t have to scramble for records—they’ve got everything in black and white.
Forklift Preventive Maintenance Checklist
Following are the 7 essential checklist items to strictly follow when conducting the preventive maintenance of forklifts:
1. Engine and Power System
- Engine Oil
-
In internal combustion engines, verify oil level using the dipstick. Ensure it’s within the recommended range.
-
Inspect for signs of oil contamination or excessive sludge.
-
Replace oil at regular intervals based on manufacturer recommendations (typically every 250-500 hours).
-
Use the specified type and grade of oil for the forklift model.
-
Inspect for leaks or signs of damage.
-
Replace the filter as per maintenance schedule or sooner if it appears clogged or damaged.
- Fuel System
-
Ensure the fuel tank is filled according to the recommended capacity.
-
Inspect for any signs of leaks around the fuel tank, lines, and connections.
-
Check for cracks, signs of wear, or leaks.
-
Tighten or replace loose or damaged hoses as needed.
-
Inspect for clogging or damage. Replace according to manufacturer specifications.
- Battery System
-
Ensure the battery is fully charged before use.
-
Check voltage level and specific gravity using a hydrometer (if applicable).
-
Clean battery terminals to prevent corrosion.
-
Tighten terminal connections to avoid loose contact.
-
Ensure the electrolyte level is sufficient.
-
Top up with distilled water if needed.
- Air Filter
-
Check for dirt and blockages. Replace if necessary.
-
Ensure the air filter is seated properly and sealed to prevent dirt entry.
-
If reusable, clean according to manufacturer instructions. Do not use compressed air unless specified.
- Radiator and Cooling System
-
Ensure coolant is within the recommended range.
-
Top up with a mixture of coolant and water if necessary.
-
Check radiator and hoses for signs of leakage.
-
Look for cracks, punctures, or corrosion.
-
Inspect the fan for smooth operation. Ensure no obstructions or signs of wear.
-
Flush the radiator and replace coolant as per the forklift maintenance schedule.
- Exhaust System
-
Check for any damage or signs of rust. Look for leaks at joints.
-
Inspect the muffler for any visible damage, rust, or leaks.
- Ensure it is securely mounted and functioning properly.
2. Hydraulic System
- Hydraulic Fluid
-
Inspect hydraulic fluid levels using the dipstick or sight glass, ensuring it’s within the recommended range.
-
If levels are low, top up with the specified hydraulic fluid.
-
Look for discoloration, signs of contamination, or foaming in the hydraulic fluid.
-
Replace fluid if it appears dirty or degraded.
-
Replace hydraulic fluid based on manufacturer recommendations, or sooner if contamination is found.
- Hydraulic Hoses and Lines
-
Check all hydraulic hoses and connections for leaks, cracks, or bulges.
-
Ensure that there are no signs of wear or damage that could lead to fluid loss.
-
Check for abrasions, cracks, and cuts in hydraulic hoses.
-
Replace any damaged hoses immediately to avoid failure.
-
Ensure all hydraulic fittings and connections are secure and not leaking.
- Hydraulic Cylinders
-
Check the seals on each hydraulic cylinder for signs of wear or leakage.
-
Replace seals if there is any sign of degradation or leakage.
-
Inspect cylinders for signs of physical damage such as dents, scratches, or pitting on the rods.
-
Clean the rods to avoid debris causing further damage to the seals.
- Hydraulic Pump
-
Look for any hydraulic fluid leaks around the pump housing or lines.
-
Test the pump’s operation to ensure smooth functionality. Listen for unusual noises or vibrations.
-
Check for signs of overheating or pressure issues.
- Control Valve and Filters
-
Check the hydraulic control valve for smooth operation.
-
Ensure that there are no sticking or binding issues with the lever or controls.
-
Inspect hydraulic filters for clogging or damage.
-
Replace filters according to manufacturer’s guidelines or sooner if needed.
3. Transmission and Drivetrain
- Transmission Fluid
-
Inspect the transmission fluid level using the dipstick. Ensure it is within the proper range.
-
Top up fluid as needed using the recommended type of transmission fluid.
-
Check the fluid for signs of contamination or degradation (e.g., burnt smell, dark color).
-
If the fluid is contaminated, replace it.
- Replace fluid as per the manufacturer’s recommended interval or sooner if the fluid shows signs of wear.
- Transmission and Differential
-
Check around the transmission and differential housing for any fluid leaks.
-
Tighten bolts and seals as needed to prevent leaks.
-
Test the transmission for smooth gear shifting. Ensure there are no grinding, slipping, or delayed engagements.:
-
Inspect the driveshaft for any visible damage or wear.
-
Check U-joints for looseness or wear, lubricating them if needed.
- Differential
-
Check the oil level in the differential. Top up with the specified oil if the level is low.
-
Look for leaks around the differential casing or seals.
-
Listen for unusual noises, such as whining or clunking, during operation, which could indicate an issue with the differential gears or bearings.
- Brake System
-
Ensure brake fluid is at the correct level. Add fluid if it’s low.
-
Examine brake lines and hoses for leaks, cracks, or damage. Replace any damaged hoses immediately.
-
Inspect brake pads and shoes for wear. Replace if they are worn down past the manufacturer’s minimum thickness.
-
Test the brakes for responsiveness. Ensure there is no sponginess or unusual resistance when applying the brake.
- Steering System
-
Inspect the fluid levels in the steering reservoir. Add fluid if necessary.
-
Check for leaks, cracks, or wear in the hydraulic steering hoses.
-
Tighten any loose fittings or replace damaged hoses.
-
Inspect the steering linkage for any play, binding, or wear.
-
Lubricate any joints or parts as required.
4. Tires and Wheels
- Tire Condition
-
Check for uneven wear or excessive tread wear that could indicate alignment issues or overloading.
-
Ensure tire tread depth meets the manufacturer’s minimum recommended depth.
-
Inspect each tire for visible damage such as cuts, cracks, or bulges that could compromise tire safety.
-
Replace tires with significant damage or structural issues.
-
Inspect for embedded debris, nails, or other objects that could cause punctures or leaks.
-
Remove any debris carefully to avoid damaging the tire.
- Tire Pressure
-
Measure tire pressure with a gauge to ensure it is within the recommended range.
-
Adjust pressure if it is too low or too high, according to manufacturer specifications.
-
Check the valve stems for leaks, ensuring there is no air loss.
-
Inspect for punctures or damage to the tire that could lead to slow leaks.
- Wheel Nuts and Bolts
-
Inspect all wheel nuts and bolts for tightness. Ensure they are securely fastened to avoid wheel detachment.
-
Torque wheel nuts to the manufacturer’s recommended specifications.
-
Check for any rust, corrosion, or damage to the wheel rims or bolts.
-
Replace any corroded or damaged parts as necessary.
- Wheel Alignment
-
Inspect the forklift for signs of uneven tire wear, which may indicate misalignment.
-
Perform alignment checks and adjustments if needed to prevent uneven tire wear and ensure smooth material handling.
- Tire Replacement
-
Monitor the tire condition regularly and replace tires when they reach the end of their service life or show signs of significant wear.
- Ensure that replacement tires meet the forklift’s load capacity and specifications.
5. Electrical System
- Battery and Charging System
-
Verify that the battery is fully charged and holding charge as expected.
-
Check the battery charging system for proper functionality, ensuring no overcharging or undercharging occurs.
-
Ensure terminals are clean, free from corrosion, and properly connected.
-
Clean the terminals with a wire brush if corrosion is found, and apply anti-corrosion spray if needed.
-
Inspect electrolyte levels in the battery cells. Top up with distilled water if necessary, especially in lead-acid batteries.
-
Check the condition of the battery cables for wear, cracks, or fraying.
-
Replace any damaged cables to avoid potential electrical shorts or failure.
- Fuses and Circuit Breakers
-
Check all relevant fuses for signs of damage or burning. Replace blown fuses with the correct amperage.
-
Ensure circuit breakers are functioning properly. Reset or replace any faulty breakers.
- Lights and Indicators
-
Inspect all forklift lights (headlights, taillights, brake lights, and turn signals) for proper operation.
-
Replace any burnt-out bulbs immediately.
-
Test all warning lights and indicators on the dashboard to ensure they function correctly.
-
Replace any faulty bulbs or malfunctioning sensors.
- Wiring and Electrical Connections
-
Examine the wiring throughout the forklift for signs of wear, fraying, or rodent damage.
-
Repair or replace damaged wires promptly.
-
Inspect electrical connectors for corrosion, loose connections, or damaged pins.
-
Clean and tighten any loose connections to prevent power loss.
- Horn and Alarms
-
Check the horn for proper functionality.
-
Replace the horn if it is not sounding correctly or is not working.
-
Ensure that backup alarms are functioning and loud enough to be heard in noisy environments.
- Replace any malfunctioning alarms immediately.
6. Fork and Mast System
- Forks
-
Examine the forks for cracks, bends, or signs of damage. Look for any signs of wear or distortion from misuse.
-
Ensure the forks are securely mounted to the carriage, with all bolts and pins tightly fastened.
-
Test the fork locking mechanism to ensure it’s functioning properly. The forks should stay in place and not shift during operation.
-
Lubricate the locking mechanism as required.
- Mast
-
Check the mast for cracks, dents, or deformation. Any structural damage to the mast should be addressed immediately.
-
Look for signs of wear or loose components that could impact the stability of the mast.
-
Ensure that the mast rails are smooth and free of obstructions or dirt buildup that could impede the lifting and lowering functions.
-
Clean the mast rails periodically to prevent debris buildup.
- Lift Chains
Inspect the lift chains for any signs of wear, rust, or stretching. Chains should be clean and free of debris.
-
Look for any visible damage or links that appear to be worn or bent.
-
Lubricate the chains to reduce friction and wear. Use an appropriate chain lubricant recommended by the manufacturer.
-
Ensure that the chains are properly tensioned. Adjust tension if necessary, based on the manufacturer’s specifications.
- Tilt Mechanism
-
Inspect the tilt cylinders for oil leaks or damage.
-
Check for smooth operation when tilting the mast. If there is jerking or hesitation, further inspection may be required.
-
Ensure that the tilt mechanism is functioning correctly. The mast should tilt smoothly in both directions without any hesitation or unusual noises.
- Hydraulic Lift System
-
Check the hydraulic cylinders for any signs of leaks, damage, or wear.
-
Ensure the seals are intact and there is no sign of oil leakage from the cylinder shaft or seals.
- Inspect hydraulic fluid for contamination, air bubbles, or discoloration. Replace fluid if necessary.
7. Safety and Operational Features
- Operator’s Compartment
-
Check the condition of the operator’s seat for any damage or wear.
-
Ensure the seatbelt is intact, functional, and securely mounted. Replace if damaged or worn out.
-
Inspect all control levers (e.g., lift, tilt, travel) and pedals for smooth operation.
-
Ensure there are no obstructions or sticky movements. Lubricate as necessary.
-
Test the horn and any other warning devices (e.g., safety alarms, flashing lights) to ensure they are working properly.
- Safety Devices
-
Inspect the overhead guard (also called the “rollover protection” structure) for any damage, rust, or structural issues.
-
Ensure it is securely mounted and provides adequate protection for the operator.
-
Verify the load backrest is intact, with no cracks or deformations.
-
Ensure it is properly secured to prevent load shifting.
-
Verify the functionality of stability systems and anti-tip devices (e.g., side stability arms, anti-roll bars).
-
Inspect for any malfunction or damage that could compromise safety.
- Fire Extinguisher
-
Ensure the fire extinguisher is present, fully charged, and free of damage.
-
Check the pressure gauge to confirm the fire extinguisher is within the recommended range.
-
Ensure the fire extinguisher has not expired. Replace if necessary according to maintenance guidelines.
- Warning Labels and Decals
-
Check all safety labels and decals on the forklift for legibility and visibility.
-
Replace any faded or damaged labels to ensure clear communication of operational instructions and safety warnings.
- Parking Brake
-
Test the parking brake for proper engagement and holding capacity. Ensure it is secure when applied.
-
Check for any signs of wear or malfunction. Adjust or repair the brake system as necessary.
-
Inspect the cables for wear, rust, or damage.
-
Lubricate or replace cables as required to ensure smooth operation.
- Safety Inspection Checklist
-
Ensure the forklift passes all safety checks and is safe to operate as per OSHA or applicable guidelines.
- Conduct a visual and functional inspection of all key safety features before each shift to confirm full operational readiness.
What are the Tips to Follow for Forklift Maintenance?
One of the key considerations of impeccable warehouse maintenance is how you maintain your forklifts as they dictate the continuity of warehouse operations. For this, discussed below are a couple of important tips to keep your forklift truck in top condition ever:
- Stick to a Routine Inspection Schedule
Carry out regular maintenance to catch problems before they snowball by checking brakes, lights, tires, and fluid levels. A consistent maintenance plan keeps unexpected breakdowns at bay.
- Keep Forks in Good Shape
Watch out for cracks, bends, or uneven wear. Damaged forks throw the balance off and put the load—and the operator—at risk.
- Don’t Let Fluids Run Low
Top off hydraulic fluid, oil, and coolant as needed. Letting levels drop too far puts stress on key components and shortens their life. Stay on top of it before trouble sets in.
- Test the Brakes Every Day
Make it a habit before each shift. Brakes that give out under load spell disaster. Catching small faults early saves both time and money down the line.
- Replace Worn Tires Without Delay
Bald or damaged tires throw the machine off balance and make it harder to steer. When rubber wears thin, it’s time to swap them out and avoid bigger headaches.
- Charge and Check the Battery Daily
A weak battery leaves you high and dry in the middle of a job. Keep terminals clean, cables tight, and charge levels where they should be to avoid unwanted downtime.
To Wrap Up
A solid forklift preventive maintenance checklist acts like a roadmap as it guides every step toward keeping your equipment in top shape. Skipping even one item on the list can send problems down the line that pile up fast.
Relying on a checklist puts you in the driver’s seat, giving control over safety and reliability instead of leaving it up to chance. It is the backbone of daily operations that keep forklifts ready to roll, day after day. So, keep your checklist close, stick to it like glue, and watch how it pays off in smooth, steady performance.